Comprehensive Guide to Transformer Insulation: Types, Structures, and Maintenance
Transformer insulation plays a critical role in ensuring the safety, reliability, and longevity of power transformers. It encompasses various types, methods, and materials designed to prevent current leakage, breakdowns, and ensure operational efficiency under diverse environmental conditions.
Types of Transformer Insulation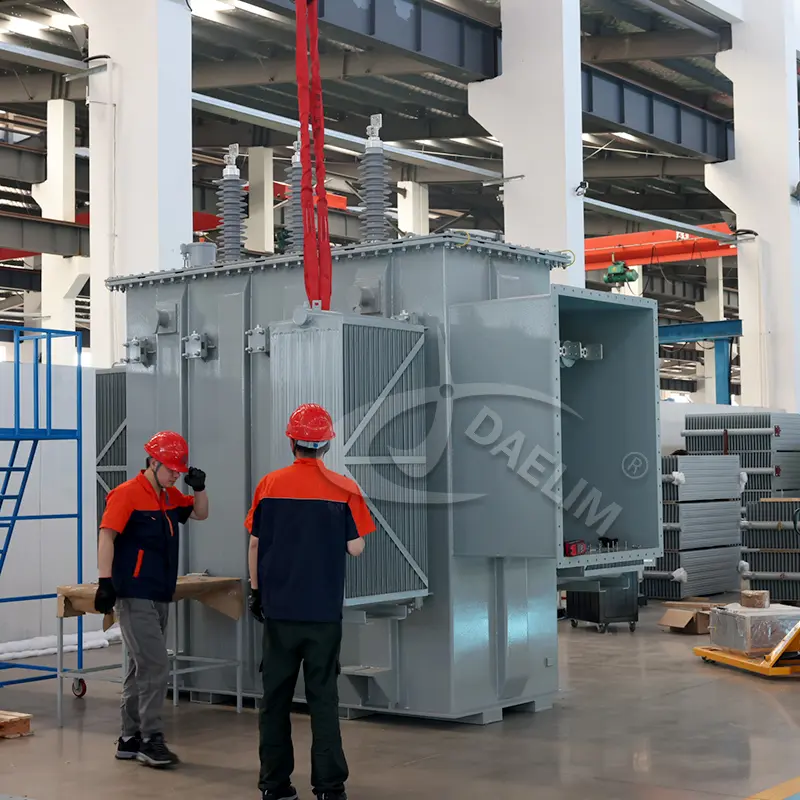
Full Insulation & Graded Insulation
- Full Insulation: Uniform insulation level across the entire winding, suitable for smaller transformers and low-capacity applications.
- Graded Insulation: Also known as semi-insulation, where the insulation near the center point of windings is lower than at the input side. Common in high-current grounding systems for voltages of 110kV and above, it reduces transformer size and costs but may compromise safety compared to full insulation.
Insulation Structure
Internal Insulation
- Main Insulation: Between windings and ground, between phases, and within windings of the same phase but different voltage levels. Critical for operational reliability and cost-effectiveness.
- Longitudinal Insulation: Ensures insulation integrity along the length of windings and components inside the transformer.
External Insulation
- Includes insulating sleeves, air gaps, and other external components that protect the transformer from environmental factors such as moisture, dirt, and atmospheric conditions.
Methods and Materials
Insulation Methods
- Oil-Immersed Insulation: Predominantly used in oil-immersed transformers for high-voltage applications, offering excellent cooling, moisture resistance, and arc extinguishing properties.
- Dry Insulation: Used in dry transformers, resistant to moisture and fire but less suitable for high-voltage environments.
- Gas Insulation: Offers low dielectric constant and effective arc extinguishing, though costly and challenging to maintain gas levels.
Insulating Materials
- Solid Materials: Include insulating papers like Nomex, Denison, and corrugated papers, offering thermal stability and moisture resistance.
- Liquid Materials: Such as insulating oils, requiring regular testing and maintenance to ensure operational integrity.
Heat Resistance Levels
- Classified into categories like Class A, E, B, F, and H, each with specific temperature limits to maintain insulation integrity under varying operational temperatures.
Common Insulation Failure Issues
Insulation Aging
- Gradual loss of mechanical and electrical insulation strength over time due to factors like moisture ingress, chemical corrosion, and prolonged overload operations. Mitigated through regular testing, cleaning, drying, and oil maintenance.
Insulation Dampness
- Causes short circuits and system damage, often due to poor sealing, transportation, installation, or maintenance practices. Prevention involves regular inspection, timely replacement of damp materials, and careful operational procedures.
Conclusion
Transformer insulation is a cornerstone of electrical safety and reliability, crucial for maintaining operational efficiency and preventing catastrophic failures. By understanding the types, structures, methods, and materials involved in transformer insulation, operators can effectively manage and maintain transformers to ensure long-term performance and safety in power distribution networks. Regular inspection, testing, and proactive maintenance are essential to mitigate risks associated with insulation aging and dampness, thereby ensuring uninterrupted and safe electricity supply.
Related Products
Related Article
Advantages of Transformer Yyn0 Vector Group
The Yyn0 vector group transformer offers distinct advantages in suppressing high-order harmonic currents and managing low-voltage single-phase ground short-circuit faults. However, it does have limitations regarding the handling of single-phase unbalanced loads, where the Dyn11 connection demonstrates superior performance. These characteristics should be carefully considered when selecting the appropriate transformer connection for specific applications to optimize performance and reliability.
Impact of Operating Temperature on Transformers
Maintaining an optimal operating temperature is crucial for the longevity and reliability of transformers. Excessive temperatures accelerate the aging process of the winding insulation, leading to a significant reduction in service life. Ensuring that the hottest point temperature remains within safe limits can help in maximizing the operational lifespan of transformers and maintaining their performance. For long-term efficiency and reliability, it is essential to monitor and control the operating temperature of transformers.
Transformer Drying Methods and Procedures
The article outlines transformer drying methods: oil tank iron loss, zero-sequence current, and vacuum dehumidification, emphasizing controlled heating and moisture removal for enhanced insulation reliability.
Transformer Oil Aging, Regeneration, and Purification
Effective management of transformer oil ensures prolonged equipment lifespan and reliable performance in electrical applications.
Technical Requirements for Transformer Installation
The article outlines critical technical requirements for transformer installation, covering support, grounding, cable management, safety measures, and fan operation to ensure safe and efficient electrical system performance.
Basic Knowledge of Transformer Transportation
Transformer transportation varies by size. Below 80 tons, use oil with dry air above oil level. Above 80 tons, use dry gas, monitor pressure, and conduct tests. Ensure sealed integrity and monitor regularly during storage.