Steps In Power Transformer Manufacturing Process
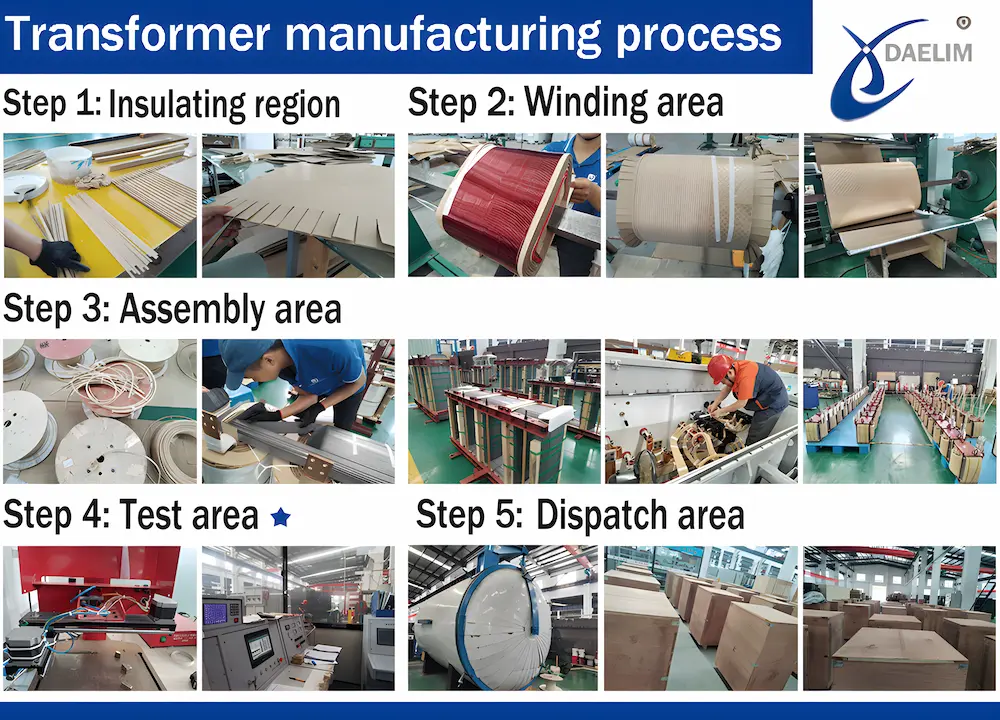
Transformer manufacturing is the process of refining a power transformer from scratch up to its final transformer assembly process. Power transformer manufacturing process is very meticulous since manufacturers carefully fabricate the whole transformer core manufacturing process and transformer tank manufacturing process.
Here at Daelim Transformer, we follow the standard manufacturing process of distribution transformers with high-quality materials exported around the globe.
Contact Daelim TransformerWhat Are The Components Of The Transformer Assembly Process?
In an electrical transformer, the magnetic core, the primary winding, and the secondary winding are the three most crucial parts of a transformer assembly process.
Other components including the body are the following:
- Insulation Lead
- Transformer Oil
- Fuel Tank And Cooling Devices
- Pressure Devices
- Protective Devices
- Bushing
When electricity flows through the main winding, magnetic flux is highly produced.
To complete the magnetic circuit, the core's flux is mainly sent through a low reluctance channel and then to the secondary cables.
Because the primary and secondary wirings share a core, their magnetic fields add together to create motion.
Laminated steel sheets with carefully measured gaps between them comprise the magnetic core of any specific transformer assembly process.
Learn more: How to test a power transformer?
What Materials Are Used In Power Transformer Manufacturing Process?
Large substation power transformers are highly constructed from the fundamental components.
These are the materials used in the power transformer manufacturing process.
- Iron for the tank
- Copper (or aluminum) for the windings
- Steel (grain-oriented) for the magnetic circuit
- Paper for the insulation
- Mineral oil for electrical insulation and thermal heat transfer
- Paint coating to protect air-exposed metal from corrosion
Many of the transformer's properties, such as type, size, and voltage range, are set by the core.
Reading more: The Ultimate Guide to Core-Type Transformers
What Is The Importance Of Transformer Manufacturing?
The use of power in the industrial transformer manufacturing process is essential in our daily lives.
No matter how large or small the field, this is vital. Every step of transformer manufacturing can be highly interrupted if there is no electricity or power.
Every component facilitating the passage of power in transformer manufacturing must be in fine working order for this to be possible.
Therefore, manufacturers currently develop and innovate transformer manufacturing so residential and commercial homes will continue to use electricity.
Try for free: Pad Mounted Transformer
What Are The Steps In Power Transformer Manufacturing Process?
During the power transformer manufacturing process, manufacturers see to it that they follow standard steps and procedures in creating a power transformer.
The work of the fabrication department ensures that the transformer's tank and radiators will be durable, high-quality, and meticulously polished.
Step 1. Transformer Core Manufacturing Process
The transformer core manufacturing process involves raw materials like silicon steel, cold-rolled with grains orientated, or CRGO.
These usually make up the bulk of the materials.
To get the desired shape of the core, thin sheets are generally bent.
The process of notching during the transformer core manufacturing process can produce a magnetic path that is significantly longer.
Then a heating process performs the circular motion applied to the laminations of the core.
Because all of the seams between the sheets are partially sealed off, the laminations during the transformer core manufacturing process are fully airtight.
The core channel frame is the part to which all of the components will be mainly attached.
In the last part of the transformer core manufacturing process, the core assembly is then held in place by these frames, which provide a robust clamping mechanism.
Step 2. Transformer Coil Manufacturing Process
After the core transformer assembly process is generally done, manufacturers can now put the core and coil together.
Then the core assembly can be set up vertically with the footplate on the floor once the manufacturers remove the top yoke.
Before varnishing, the core's limbs are firmly wrapped in cotton tape.
Upon the transformer manufacturing coil process, manufacturers separate the arms of the core and then connect it to a low-voltage coil.
It is necessary to make use of oil ducts to keep the required vertical and horizontal space between coil segments during the coil's transformer assembly process.
After that, bolts and rods are mainly used for the majority of the top frame's fastening. Then manufacturers connect the coil windings either in series or in parallel.
When it is necessary to do so, they install barriers may between HV phases during the coil transformer assembly process.
If they are going to use the tapping switch, the wiring should be always in place. After they finish the core coil transformer manufacturing, they put it into a drying oven.
Step 3. Transformer Tank Manufacturing Process
Some transformer manufacturers like Daelim only utilize high-quality steel in all their storage tanks.
That is to pass the rigorous inspections necessitated by both international standards and the client.
After the core-coil assembly is generally removed from the oven, an insulation resistance test is mainly carried out to perform the transformer tank manufacturing process.
The insulating resistance value must be within specification to proceed with the assembly.
Before delivering the tanks to the tank-up section for final assembly, the fabrication department finishes painting them.
A drain valve, conservator, oil level monitor, and explosion vent are all part of the standard equipment under the transformer tank manufacturing process.
Here, we'll be making sure the core-coil assembly stays put inside the tank.
Afterward, the tank will be full of filtered, pure transformer oil, which completely submerges the transformer.
In the last stage of the transformer tank manufacturing process, each terminal bushing has a cable running from it to the first and second connectors.
Step 4. Transformer Painting And Finishing Manufacturing Process
At this stage of the power transformer manufacturing process, standard tank cleaning procedures involve grinding.
Seven-tanks phosphate cleaning materials are generally applied to scrub the tank's exterior.
Manufacturers apply a special paint that can withstand extremely high temperatures. They spray it inside the tanks after they have been carefully cleaned.
Afterward, they use an epoxy powder coat or primer and apply it to the exterior of the tank. They spray a single layer of enamel during this time of transformer assembly process.
The accuracy of the final product is thoroughly checked against the customer's requirements and the drawings used in the design of the power transformer manufacturing process.
Each transformer undergoes an air pressure test to rule out the possibility of leaks or seepage. The transformer's oil level corresponds to the lowest line.
For the last method, manufacturers secure the security of all components, from dial temperatures to connections to earthing terminals.
Step 5. Transformer Testing Manufacturing Process
In this last stage of the power transformer manufacturing process, manufacturers seal the transformer tank.
Then they begin several testing and inspections of the transformer.
- The windings of a transformer are highly tested for their resistance.
- Checking the Transformers' Ratio for Accuracy.
- Verifying the Vector Class of Transformers.
- Measurements of load loss and the voltage across impedance.
- Conducting an insulation material analysis.
- Evaluating the dielectric properties of a transformer.
- Testing a tap-changer while it is under pressure.
During the testing of the power transformer manufacturing process, manufacturers do an open circuit test.
This is where the current and resistance of the transformers are properly measured with no load present.
Overall, manufacturers should not forget this last stage of the power transformer manufacturing process which is examining for leaks around the gaskets and couplings.
You may enjoy: Ultimate Guide to Utility Transformer
What Is The Final Stage of the Transformer Assembly Process?
In the last stages of the transformer assembly process, the core and coils are generally cooled by condensing the vapor around them.
After the interior of the tank has been thoroughly dried, it is then compacted to an engineering-mandated pressure.
All electrical clearances are triple-verified, and all metal and fiber fasteners are torqued or tightened to the correct specifications.
Thereafter, oil is heavily poured into the tank to prevent air leakage and the lid assembly is then attached.
At this stage of the transformer assembly process, then bushing connections are highly made after the core and coil assembly has been mainly positioned inside the tank.
The next step goes as the unit is primarily emptied, and a vacuum is mainly pumped into the transformer.
Next, manufacturers check if there are potential leaks.
During this transformer assembly process, manufacturers also install wiring for the customer's selected control panel and any additional screens and devices.
For the last stage of the transformer assembly process, all external weld components are mainly welded in place before they ship out the unit shipped for factory acceptance testing.
Read my article on The Ultimate Guide to Pole-Mounted Transformers
What Are The 3 Types of Transformer Testing During the Power Transformer Manufacturing Process?
These are all the testing and inspection necessary during a power transformer manufacturing process.
Routine Tests
At this stage of the power transformer manufacturing process, performing routine tests on transformers guarantees that the entire production run.
Every manufactured good must pass a series of quality assurance inspections.
Special Tests
To gather information that will be helpful during operation and maintenance, customers can request specialist testing of their transformers.
Pre Commissioning Test
Before you can use a transformer in operation, a comprehensive series of testing must be highly carried out.
It is common practice to put a transformer through a pre-commissioning test before putting it into service.
Every low-voltage test result is double-checked against factory test data to determine the transformer's health after installation.
Learn more about Transformer Test
What Is The Importance Of Assessment And Inspection During Transformer Assembly?
The transformer undergoes rigorous assessment and inspection at the factory during the power transformer manufacturing process.
This is to ensure it will function and will satisfy the needs of the end user.
Multiple tests must be highly performed on a transformer to verify its primary function.
Prototype versions, as opposed to mass-produced devices, are always used for these kinds of assessments.
During the transformer assembly process, a transformer inspection ensures that a batch of transformers meets the very minimum requirements for functioning properly.
Try for free: Transformers Solution For Data Center and Cryptocurrency Mining
Why Factory Acceptance Test Checklist Is Necessary For Transformer Manufacturing?
When it comes to transformer manufacturing, having a factory acceptance test checklist is essential.
Each power transformer is always subjected to a battery of testing before it may be generally used to generate electricity.
The buyer oversees testing at the plant before moving on to the installation site for a final inspection.
Afterward, the manufacturer provides a complimentary pre-shipment inspection and pays for any necessary testing of materials.
Many manufacturers seek to either avoid or cheat on examinations after the transformer manufacturing process.
Because the vendor can tailor the set of tests to his specifications.
Therefore, testing methods and the optimal approach are important to ensure a transformer's longevity.
Get it now: Pole Mounted Transformer
What Are The Maintenance Procedure For the Manufacturing Process Of Distribution Transformers?
After the manufacturing process of distribution transformers, it is important to check them thoroughly for any transportation damage.
This is especially true when receiving new power transformers.
Before unloading, make sure nothing was impartially broken in transit by hard handling, and file a claim with the carrier and the manufacturer if necessary.
After that, you need to have a look inside to make sure nothing has moved, the porcelain is not broken, there is no dirt or other debris, and there is no standing water or dampness.
Users and consumers must take corrective measures if necessary.
If you have transport braces, you should throw them away after use.
After relocating or storing a transformer, it must be highly verified once more before turning it on for the first time.
Which Manufacturer Pass All Standard Quality of Transformer Manufacturing?
Daelim Transformer is the industry leader in electrical transformers since its products consistently pass end-to-end testing during the power transformer manufacturing process.
Furthermore, Daelim transformer's power transformers aren't shipped to customers unless they pass rigorous testing and quality assurance inspections.
The transformers we send out meet the highest quality standards because of our strict quality control measures.
To make sure that no part of the transformer is highly missed during testing, we provide a factory inspection checklist.
Daelim's ability to oversee every stage of production ensures high-quality results for our transformers.
To inspect and test the transformer's key components, we have a fully equipped factory based in China.