Key Principles of High Voltage Transformer Design
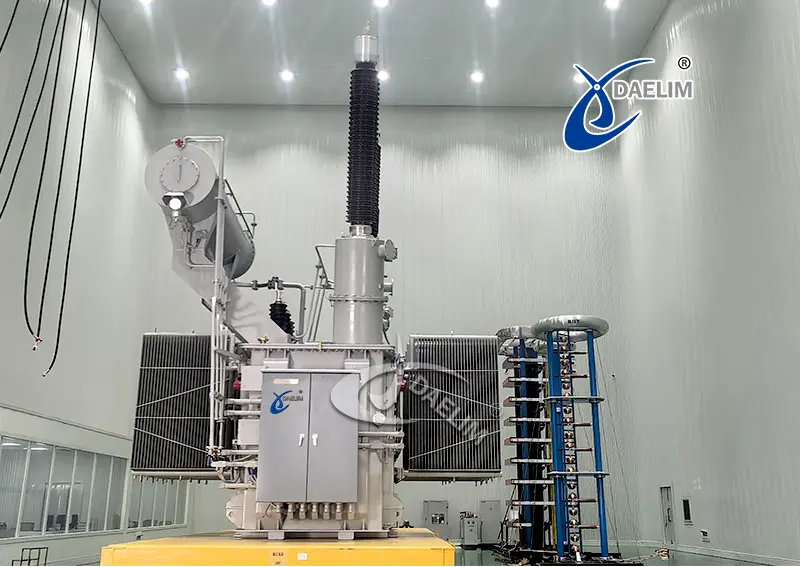
Our industrial world needs hundreds of thousands of megawatts of electricity every day. Electricity that cannot be produced on-site and a system is needed to transfer that electricity from production units to the thousands of industries that need it. This is where our electrical transformers work to regulate electricity.
The high voltage transformer design is such that it can facilitate the regulation of several hundred megawatts on electricity 24/7 without any need for regular maintenance. Today we will explain each and every aspect of high voltage transformer design so you can have a very deep understanding of these transformers.
Contact Daelim Transformer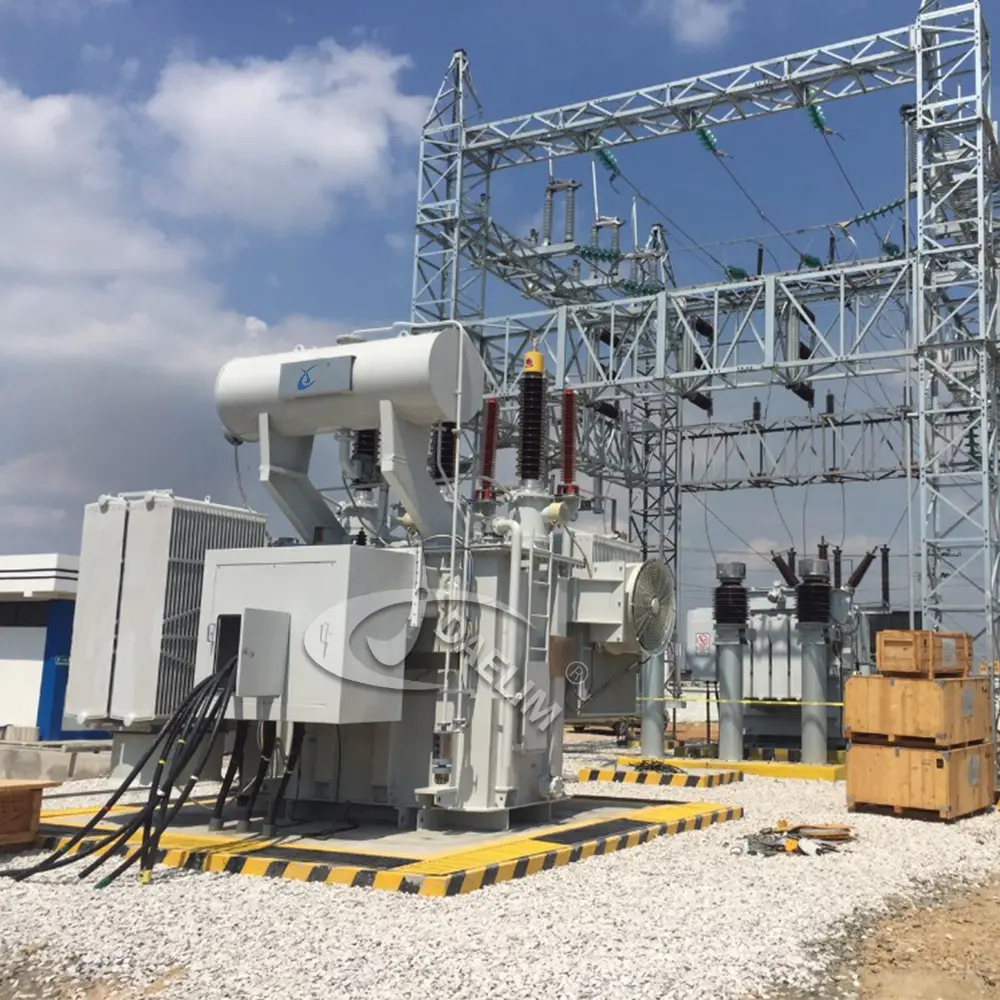
- Primary Voltage Ratings: 115 kV
- Secondary Voltage Ratings: 34.5 kV
- H.V. TAP RANGE: 115kV*+/- 16 x 0,625 %
- CONNECTION TYPE: YNyn0d1
- Standards: IEC
- Application: 115lV Substation
- Power Rating: 31.5MVA/36MVA
- Cooling Method: ONAN & ONAF
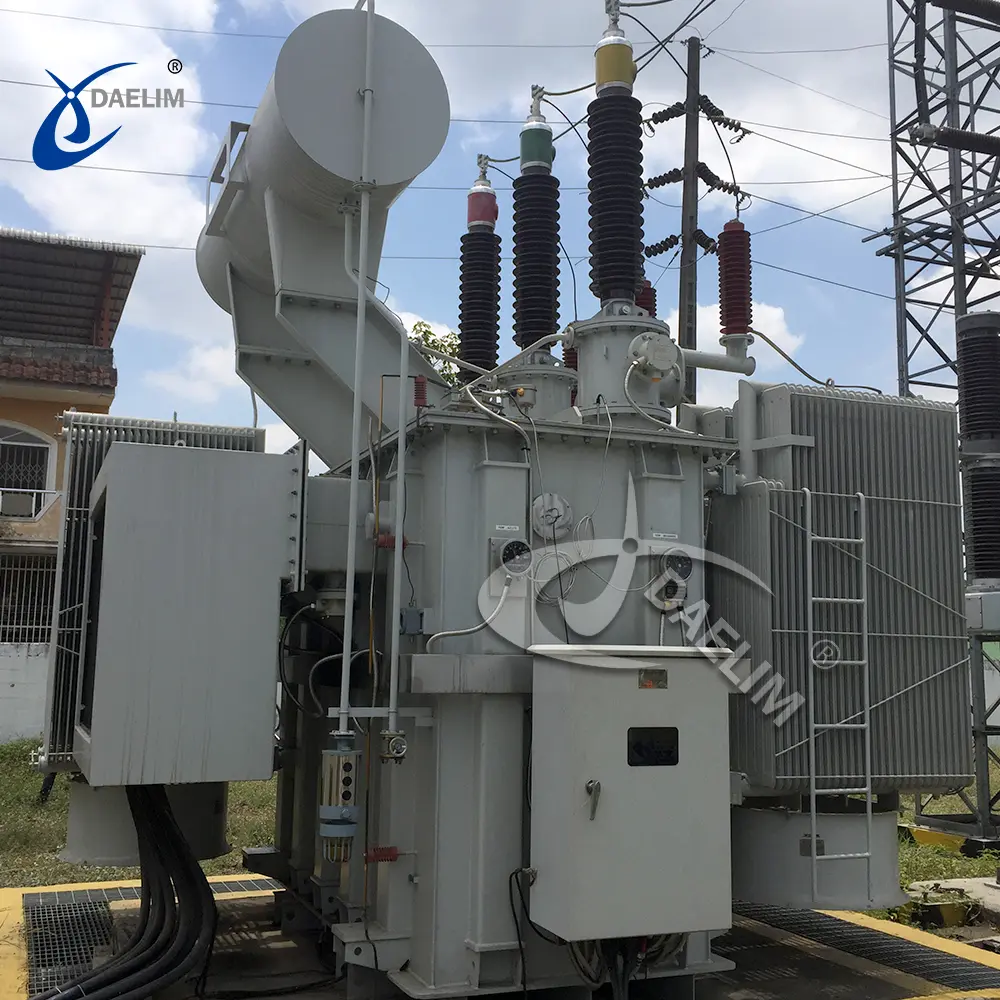
- Primary Voltage Ratings: 69 kV
- Secondary Voltage Ratings: 13.8 kV
- H.V. TAP RANGE: ±8*1.25%
- CONNECTION TYPE: YNhd
- TYPE: 3 phase
- Application: 69kV Substation
- Power Rating: 30MVA & 35MVA
- Cooling Method: ONAN & ONAF
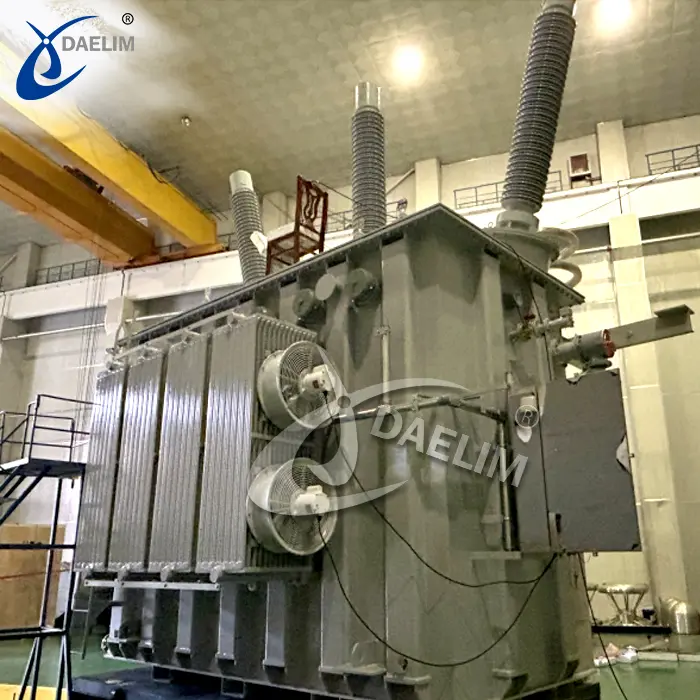
- Primary Voltage Ratings: 220 kV, 230 kV or others
- Secondary Voltage Ratings: 69/35/37/34.5/26.4./11/10.5/6.6/13.2 kV or others
- H.V. TAP RANGE: ±8×1.25% or others
- CONNECTION TYPE: YNd11 or others
- Standards: IEEE, CSA, IEC
What is a High Voltage Transformer?
High voltage transformers are like any other transformer with one basic difference and that is the power they regulate. High voltage transformer is a type of transformer that regular electrical power anything above 35 kV and a capacity greater than 10 MVA.
These high voltage transformers are extensively used in power transmission where they are responsible for stepping up power from grid stations and stepping down power at local grid, before distribution to local consumer installations.
They are also used in large industries that have very high power consumption and need a dedicated high voltage transformer for smooth working. These industries include manufacturing plants, steel or iron melting plants or testing laboratories that test different high voltage equipment or environments.
Due to such a high power regulation, no ordinary part or materials can be used in these transformers. So high voltage transformer design is state of the art and materials used are truly unique.
Key Principles of High Voltage Transformer Design
1. Core Design
Transformer core is one of the most crucial parts of a transformer. It is responsible for transferring magnetic flux between transformer windings. In high voltage transformer design, the transformer core design and core material are the two crucial factors.
As high voltage transformers are dealing with megawatts of power, the core losses associated with a regular transformer core will be huge. So special core designs like toroidal and laminated core designs are used. Selection of design is also heavily influenced by the application and space constraint.
A regular transformer core is made from silicon steel or amorphous metals but low grades of these materials will not be able to resist the heat and transfer magnetic flux efficiently. Due to this reason only high grade silicon steel specially grain oriented electrical steel is used in high voltage transformer core design. Some common grades are M3, M4, M5, M6 with ASTM A677 or IEC 60404 standards specifications.
Another advanced material used in transformer cores is amorphous metal alloys. This includes Metglas 2605SA1 and Hitachi Finemet. These alloys have a non crystalline structure, offering exceptionally low core losses. This is due to their high resistivity and thin laminations, typically 25 to 50 microns thick. Amorphous metals are used in high efficiency transformers where energy savings are a priority.
More resource: The Crucial Role of Iron Cores in Transformer Design and Function
2. Winding Configuration
Working of a regular and a high voltage transformer winding is the same. They both work to either step up or step down the input voltage. Both winding use 99.99% pure copper as materials. The difference lies in how much voltage each transformer deals with.
A high voltage transformer basically deals with thousands of bolts and thus needs a special insulation technique and material. Advanced and quality insulation materials like polyimide films, nomax and polyester films are used between different layers of the winding.
Polyimide films such as Kapton are utilized for their exceptional thermal stability and dielectric strength. This film can withstand temperatures up to 250°C. These are also resistant to moisture and chemical exposure. This makes them ideal for compact design transformers.
Similarly nomex is used in applications where both thermal and electrical stability are paramount. With a thermal resistance of up to 220°C it provides excellent mechanical strength and low moisture absorption. This makes it suitable for layer insulation and conductor wrapping.
Learn more about Transformer Winding
3. Insulation Systems
The complete set of high voltage transformer core and winding are needed to be insulated from external environmental factors like moisture and dust. In regular size transformers oil based systems and epoxy resins are used to insulate the transformer winding from the external environment.
Same oil based and epoxy based systems can be used for insulating high voltage transformer winding but oil or epoxy used in regular transformers cannot be used in these transformers.
Other than the use of specific insulating systems, Adequate spacing and layering are critical to handling high voltage stress.
Reading more about Transformer Insulation
4. Cooling Mechanisms
The complete set of high voltage transformer core and winding are needed to be cooled as a lot of heat is produced during regulating extremely high voltage. Due to the immense heat being produced during the high voltage regulation, a dedicated heat exchanger based cooling mechanism is used in high voltage transformer design.
These systems are basically oil based systems but unlike conventional systems where core and winding are kept immersed in oil inside the transformer tank, this system force circulated the oil through heat exchanger.
Oil absorbs heat from the transformer core and winding. That oil is then forced by the oil pump to pass through the specialized design heat exchanger. Heat from the oil is then removed using either forced air flow or a dedicated coolant based refrigeration system.
Cooled oil is then moved again in the transformer tank where it is worked to absorb heat from core and winding.
Design Considerations for High Voltage Transformers
1. Operating Frequency
Each transformer can handle a range of frequency at which electricity is being provided to and transmitted from the transformer. The operating frequency has an inverse relation with the size and efficiency of the core.
Higher the operating frequency of the transformer, smaller can be the size of the core thus higher efficiency can be achieved. This came with a side effect and that the smaller core heats up quicker than large size core and thus needs insulation issues due to increased thermal stress.
So when discussing the high voltage transformer design, it's important to understand the power rating and frequency at which the power will be transmitted and insulating issues that might get in the way.
2. Load Requirements
Each high voltage transformer is designed to regulate a range of voltage and in that it has an operating voltage and maximum operating voltage. The operating voltage is that at which the transformer works most of the time and maximum operating voltage is one above which safe operation of the transformer is not guaranteed.
When working on the high voltage transformer design, it's important to know the specific load profiles required without overheating or reducing efficiency of the transformer. Load factors also determine the thermal rating of the device. Thermal rating is temperature which transformer insulation, oil and cooling systems can resist safely.
3. Safety Standards and Regulations
Another important factor to consider for high voltage transformer design is the related safety standards and regulations. It is important to adhere to the international standards, such as IEC 60076 and ANSI/IEEE C57 to ensure safety, reliability, and environmental compliance.
Keep reading:Transformer Design: Step by Step Guide for Safety and Reliable Power Flow
Challenges in High Voltage Transformer Design
High voltage transformer design offers challenges of its own. Depending on the size and power rating of these transformers, following are three main challenges of high voltage transformer design.
- High voltage transformers regular megawatts of electricity through their windings. This results in very high voltage stress that can lead to premature insulation failure. So use of only very high quality insulation and regular inspection or maintenance is required.
- Regulating megawatts of electricity produces a lot of waste heat that can cause problems in transformer thermal management. Care must be taken during the design stage and inspection is needed for managing heat generated under load and preventing hotspots.
- Electromagnetic forces produced due to high current flows in transformer winding can be so strong in high voltage transformers that it can bend or break any weak metallic part. As these forces can attract or repel metallic parts, a robust mechanical design is needed for these transformers.
Future Trends in High Voltage Transformer Technology
Advance Material
As stress and heat associated with High voltage transformers is so high that it needs dedicated materials for high efficiency. So to advance further and push design of high voltage transformers development of high-temperature superconducting materials is needed. Improved insulation systems are also needed for enhancing efficiency and reliability of these transformers.
Smart Transformers
One of the best advancement in high voltage transformer design will be the integration of IOT and AI technologies. This will enable them to enable real time monitoring, predictive maintenance, and better grid management for electricity companies and industrial installations.
You may enjoy: Smart Substation
Sustainability
As future trends of almost all items has sustainability as a compulsory part, so eco-friendly designs, such as biodegradable insulation fluids and reduced core material usage, are gaining traction to meet global environmental goals
Try for free: FR3 Oil vs Mineral Oil Transformer
Conclusion
High voltage transformers are indispensable for modern power systems. They ensure the safe and efficient transfer of energy. By adhering to design principles, addressing challenges, and embracing innovation. This industry continues to enhance the performance and sustainability of these critical devices.
Follow Up
Empowering industries across America, Europe, Oceania, and others around the globe, Daelim is your trusted partner for high performance high voltage transformers. Renowned for cutting-edge technology, exceptional durability, and energy efficiency, we offer high-voltage power transformers that range above 345kV and 500 MVA in capacity and meets diverse industrial standards including ANSI, IEEE, CSA, AS, GOST, IEC, EU, DIN/VDE. We also offer all types of high voltage transformer repair & maintenance, installation, testing, on-site support services.
Contact Us with your query and our team will talk you through the process.
Related Products
Related Article
Canadian 69 kV Substation Transformer Project
Today, we are excited to present a case study on a 69 kV substation transformer project by Daelim Transformer. Our Canadian client required a step-down transformer for their substation to connect with the hydroelectric grid in Quebec.
69 kV Power Transformer for Substation in Pennsylvania
Daelim recently completed the design, supply, and installation of a custom 69 kV transformer for a substation in Pennsylvania. This high-efficiency, three-phase transformer is engineered for reliability, scalability, and long-term performance, ensuring a stable power supply to the substation. Key features include low load losses, minimal maintenance, high insulation levels, and flexible cooling options. The solution enhances grid stability, supports future expansion, and minimizes energy consumption, reinforcing Daelim’s commitment to quality and innovation in power systems.
230 kV Three Phase Power Transformer For USA Market
In 2023, Daelim Transformer designed and manufactured a cutting-edge 230 kV three-phase power transformer for a client in Nevada, USA. The client recently shared installation and operational photos, showcasing the successful deployment of this remarkable transformer. Let's delve into the specifics of this transformer project!
13.8 kV 10.5 MVA Substation Transformer for Ecuador
A customer from Ecuador contacted Daelim Transformer for a 10.5MVA substation transformer (13.8kV high voltage, 2.4kV low voltage). Daelim Transformer provided a customized solution, conducted virtual factory tours, ensured rigorous quality control via video inspections, and offered post-delivery online training and ongoing support, fostering a successful partnership.
Empower Your Data Center with Daelim Transformer
Daelim Transformer provides reliable and efficient transformer solutions for data centers, ensuring high power capacity, safety, and energy efficiency. With customized options such as oil-immersed, dry-type, and smart transformers, Daelim addresses critical needs for redundancy, power quality, and load management. Our transformers offer high reliability, scalable designs, and advanced cooling methods, supporting modern data centers with high-density IT equipment. With ongoing maintenance and monitoring services, Daelim ensures continuous, optimal performance for data centers worldwide. Contact Daelim today to power your data center with confidence.
20MVA Power Transformer for the United States
This project involves the development of a 20 MVA three-phase power transformer tailored for the United States market. The primary voltage is 24.94kV, and the secondary voltage is 4.16kV, indicating it functions as a step-down transformer. The design and production fully comply with IEEE C57.12.00 standards and have passed third-party UL team testing. All accessories also adhere to IEEE standards. FR3 vegetable oil serves as the insulating liquid for the transformers.