VPI Transformer vs Cast Resin
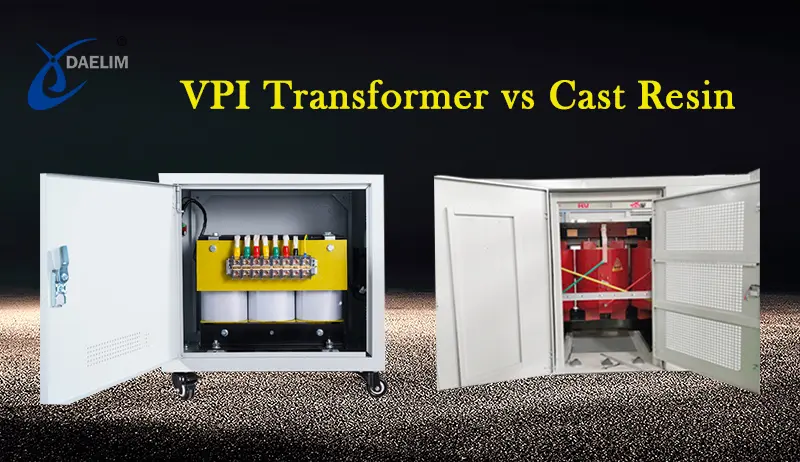
Dry type transformers are widely used in industry due to their high efficiency, compact design, and very low maintenance. Among dry type transformers, two specific transformers: Vacuum Pressure Impregnated Transformer (VPI transformer) and Cast Resin Transformer are the most popular ones.
This article delves into the key difference between Cast Resin and VPI transformers. Explaining their benefits, applications, and considerations for choosing between VPI transformer vs Cast Resin Transformers.
Contact Daelim TransformerKey Differences Between VPI Transformer vs Cast Resin
This comparison is not only about writing VPI transformer vs cast resin which is better, rather is a comprehensive discussion on how each type performs in certain scenarios.
Definition and Construction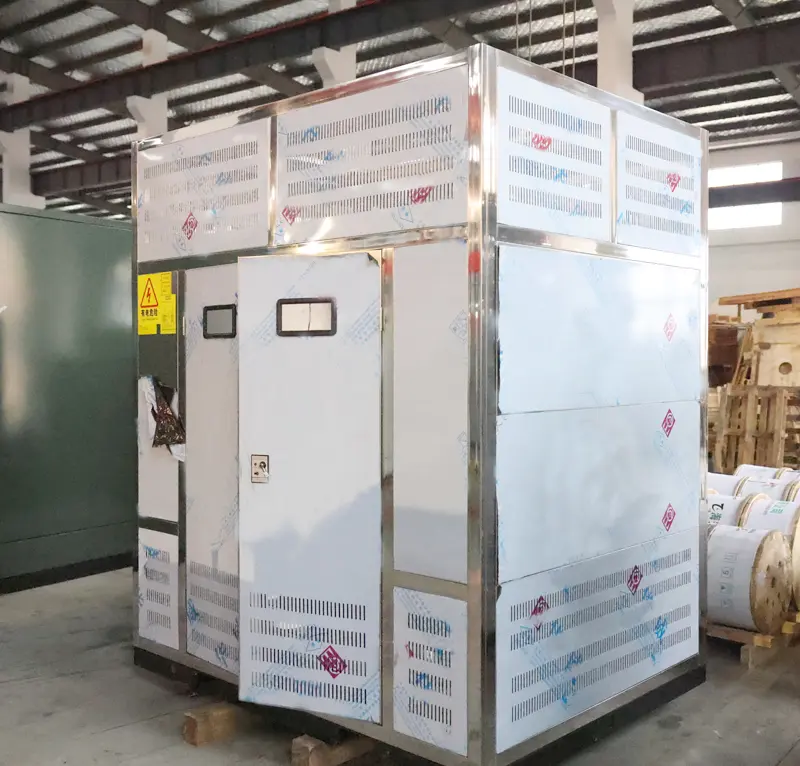
Vacuum pressure impregnated transformers are the dry type transformers. These transformers are constructed by impregnating the transformer winding with a resin under specific vacuum pressure conditions. The cast resin transformers are also dry type transformers. These transformers are also constructed by encapsulating the transformer winding into an epoxy resin but without the application of vacuum pressure.
The vacuum pressure in VPI transformers ensures that the resin fills all the spaces of transformer winding. This process enhances insulation and mechanical strength while protecting the windings from environmental exposure.
Opposite to this, in cast resin transformers, epoxy resin is poured to the transformer winding to completely cover the transformer winding layers and core. This offers excellent insulation and protection against contaminants.
The epoxy resin has to be cured by heating the epoxy covered transformer winding in a process called epoxy potting. The VPI transformer also needs heating and curing of its resin along with vacuum pressure.
In VPI transformers high grade resins and insulating varnishes are used for covering and insulating the transformer winding whereas in cast resin epoxy resin and fiberglass reinforcement is used for insulating the winding.
Vacuum pressure in VPI transformer ensures a compact and open winding structure that has a robust varnish coating whereas the fiberglass reinforced epoxy resin coating in cast resin transformer ensures a solid casted construction on winding that offer high thermal endurance.
Advantages and Drawbacks of VPI and Cast Resin Transformers
Due to application of vacuum pressure in the VPI transformer manufacturing process,a layer of resin is made on the entire winding and core. The quality of the insulation produced is very good and it offers good moisture resistance and is effective for only moderately harsh environments.
In cast resin transformers a solid casted construction is made on the winding that makes winding exceptionally resistant to moisture, dust, and chemicals, making them ideal for extreme environments.
Vacuum application also made a compact winding design with high strength in VPI transformer but solid construction of resin in cast resin transformer that has been reinforced with fiberglass excel in impact and compressive load but not much against vibrations.
Due to compact and open winding design with a layer of resin on it, VPI transformer can be repaired for any damage due to extensive use or harsh environment. In cast resin transformers, due to a rigid cast construction, no repair can be done in case of any damage.
Cast resin transformer epoxy has the tendency of shrinking over time, this can lead to potential transformer winding short circuit and thus failure of the entire transformer as cast resin transformer winding cannot be replaced.
Applications of VPI Transformer vs Cast Resin Transformers
Due to their advantages of compact and open design winding but limitation of resistance against moderately harsh environments, the VPI transformer has application in Industrial facilities with moderate conditions.
Applications like metal manufacturing plants, machinery and equipment assembly units, industrial product warehouses and distribution centers, processing units and even commercial large residential buildings with HVAC systems, VPI transformers are the best investments.
All these applications have a low to moderate harsh environment. Most importantly these applications need a balance of durability and cost effectiveness. With low initial cost and ability to repair, cost effectiveness makes them ideal for all types of small to medium size industrial installations.
Moreover these transformers handle medium power loads efficiently, making them suitable for facilities that require steady but not extreme performance.
Cast resin transformers are designed for extreme conditions keeping safety requirements in mind. This makes them indispensable in environments where environmental and operational challenges are severe.
Applications like marine, mining and offshore installations where there are extremely harsh conditions like humidity, corrosive environment, and extreme temperature fluctuations, cast resin transformers are an ideal option. Due to their solid cast robust construction they can resist all types of environmental factors including saltwater and saline air.
Manufacturing Process
The steps involved in both transformer manufacturing are very much common. Both transformers need resin for insulation purposes and both transformer winding goes through the process of resin curing. The approach of applying the resin is what makes all the difference.
In VPI transformer manufacturing, transformer winding is placed inside a mold and high grade resin is introduced into the mold with the application of vacuum pressure. The entire process is done with automated machines which make this process highly efficient and product uniform across the entire production volume.
In cast resin transformer manufacturing, transformer winding is placed inside a mold and epoxy resin is introduced into the mold. Heating and curing is done inside the mold to solidify the resin. The steps of applying fiberglass layers for reinforcement is completely manual and is very labor extensive.
Due to the nature and steps involved in VPI transformer manufacturing, the entire process can be fully automated. This increases the production rate and reduces manual labor. This reduces the final cost of the VPI transformer.
Opposite to this, cast resin transformer manufacturing process can be partially automated which slows down the production rate and increases the final production cost.
You may enjoy: Steps In Power Transformer Manufacturing Process
Performance and Durability
If the performance and durability of these two transformers are considered individually or when compared to the oil filled transformers. Then both these transformers have high performance and are quite durable.
If performance and durability of the both are compared with each other, then in areas with space constraint and with a moderate harsh environment, VPI transformer will be better in performance and durability and it has compact design with excellent insulation against moderate harsh environment.
VPI transformers generally have a shorter lifespan compared to cast resin models in harsh conditions. Cast resin transformers are more reliable in environments prone to high moisture and pollutants.
Safety and Environmental Considerations
As both transformer types regulate huge electrical power ranging from several kVA to MVA and both are being used widely in various industries. So their safety and environmental impact needs to be considered and compared during this comparison.
VPI transformers due to their vacuum application produce a perfect layer of resin on winding that gives excellent insulation and prevention against short circuit but is not highly effective against fire. Varnish used with resin reduces the flammability of the layer but does not make it completely non-flammable.
On the other hand, epoxy resin with fiberglass reinforcement has high fire resistance. The encapsulated resin is self-extinguishing and minimizes fire hazards. This also gives the cast resin transformer a high resistance against thermal overload as compared to the VPI transformer. Due to the shrinking nature of epoxy, the tendency of the short circuit is always higher in cast resin compared to VPI transformers.
When considering the environmental impact, VPI transformers are a bit easier to dismantle when compared to cast resin transformers. Both need specialized tools and techniques but a thin layer of resin with varnish is just easier to handle and decompose better as epoxy resin which is not biodegradable.
When considering material toxicity, use of varnish in a VPI transformer can emit volatile organic compounds when subject to extreme thermal stress. Epoxy resin is highly stable against extreme thermal load so it is not considered dangerous during operation but disposal is environmentally concerning.
At the end of life both transformers insulating materials are very difficult to recycle and are usually disposed of in a landfill.
Short Comparison of VPI Transformer vs Cast Resin Transformer
Feature | VPI Transformers | Cast Resin Transformers |
Durability | Moderate | High |
Cost | More cost-effective | Higher upfront cost |
Environmental Resistance | Suitable for moderate environments | Ideal for harsh conditions |
Fire Resistance | Limited | Excellent |
Typical Applications | Industrial facilities, moderate conditions | Marine, mining, indoor sensitive areas |
How to Choose Between VPI and Cast Resin Transformers
Choosing the right transformer from VPI transformer vs cast resin transformer depends on factors like environment, fire risk, budget and operation cost, and any other specific industry needs.
Environment
Cast resin transformers are best for extreme environments where humidity, dust, and heat are usually very high. Opposite to that, in a clean environment with moderate humidity, dust, and heat, VPI transformers are highly commended. This is due to their greater efficiency and open winding design ensuring rapid heat removal without the need of a cooling fan.
Fire Risk
All those installations where fire risk is high or any fire can cause severe damage to the primary operation of industry, cast resin transformers are best. Their resin has a non-flammable nature and can resist high temperatures.
Budget
When comparing VPI transformer vs cast resin price, In all those industries or commercial and residential installation where initial cost of installation is limited with a limited budget to operate and maintain the transformer. VPI transformers are highly recommended as they are cost effective and can be repaired for minor damages.
Cast resin transformers are little expensive but are highly durable. They usually do not need much maintenance and can be considered cost effective in the long run. There is one serious disadvantage, any damage to winding cannot be repaired and can only be replaced.
Industry Requirements
One major factor is the industry requirements like power rating, noise and vibrations, environment concerns, availability of space, and adaptability of existing infrastructure. These factors play an important role in transformer selection.
It is highly recommended to have a comprehensive study of all industrial needs and other factors influencing the transformer selection before making a decision.
Conclusion
VPI transformer vs cast resin transformer was done to help you understand who these transformers are best in their respective setups. VPI transformers have better insulation and offer open winding design that help do minor repairs at lower cost. Cast resin transformers are durable and can resist extreme environmental conditions but are not against vibrations. Their epoxy can shrink over time thus causing a probability of short circuit.
Follow Up
Selecting the wrong type of transformer for your industry can affect your operations. Daelim offers dry type transformers that deliver far better performance than any other available oil type transformer. We have VPI transformers and cast resin transformers of all sizes and power ratings.
Daelim's commitment to standards like ANSI, IEEE, CSA, AS, GOST, IEC, EU, and DIN/VDE in transformer manufacturing and supply has developed a strong customer base in the USA, Europe, Canada, Australia, and all others around the globe. If you have any query about VPI transformers or Cast Resin Transformers, just Contact Us and we will talk you through the process.
Related Products
Related Article
VPI Transformer
VPI transformers are high-performance, environmentally friendly, and low-maintenance transformers, ideal for industries requiring reliable power distribution. They feature vacuum-pressure impregnated windings for superior insulation, thermal endurance, and extended lifespan. VPI transformers offer reduced noise, improved efficiency, and are available in multiple power ratings, making them suitable for manufacturing, renewable energy, critical infrastructure, and marine applications.
Cast Resin Transformer: Definition, Types, Benefits, Applications, Maintenance
The cast resin transformer is a type of dry transformer that uses epoxy resin to encapsulate the windings and core, providing excellent insulation and environmental protection.
Key Principles of High Voltage Transformer Design
High voltage transformers are crucial for efficient power transmission, stepping up or down voltages above 35 kV and 10 MVA. Their design involves advanced materials, including high-grade silicon steel and amorphous metals, along with specialized insulation and cooling systems. Key challenges include managing high voltage stress, heat, and electromagnetic forces. Future trends focus on smart technology integration, sustainability, and advanced materials for enhanced efficiency.
Aluminum vs Copper Transformers
Copper transformers are more efficient, durable, and better at heat dissipation, making them ideal for high-load and long-term industrial applications. Aluminum transformers, while more cost-effective and lightweight, are less efficient, prone to wear, and better suited for low to moderate loads in residential or small-scale uses. Hybrid systems combine both materials for optimized performance and cost-efficiency.
Transformer Shortage: Factors and Challenges of Current World Order
The global shortage of electrical transformers is driven by increased demand due to lifestyle shifts, population growth, and industrial expansion, particularly in electric vehicles, cryptocurrency mining, and AI data centers. National policies, supply chain disruptions, raw material shortages, and manufacturing constraints further exacerbate the issue. Daelim offers industry-focused solutions, leveraging multiple production facilities to meet demand and provide high-quality transformers in record time.
How to Ensure Safe Transformer Storage
Proper transformer storage is crucial for long-term reliability. Key steps include choosing a stable, weather-protected location, sealing openings, maintaining nitrogen pressure for liquid-filled transformers, and ensuring dry conditions for dry-type transformers. Regular inspections, moisture monitoring, and pre-service testing ensure optimal performance. Proper care prevents damage, extending transformer lifespan and reducing maintenance costs.