Manufacturing of Large Power Transformer
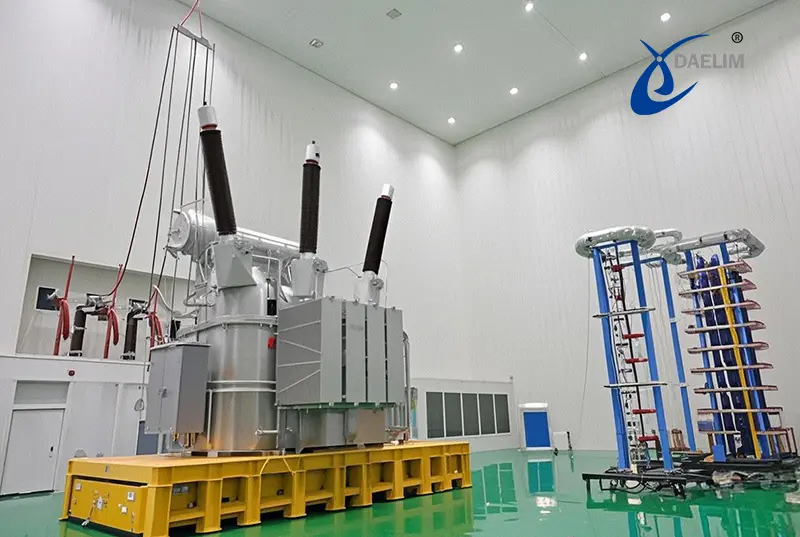
Large power transformers are a key part of our electrical power generation and distribution system. If you talk about the large power transformer and the US electric grid, then you will know that large power transformers are the first step in US electricity distribution from the electrical grid to consumers. Performance, efficiency, and reliability of these electrical power transformers is so important that large power transformer manufacturers keep this in mind at every stage of design and development of these electric transformers.
This article is dedicated to understanding the manufacturing process of large power transformers. We will discuss each and every process involved in manufacturing of different parts of the electrical transformer.
Contact Daelim TransformerLarge Power Transformer Manufacturing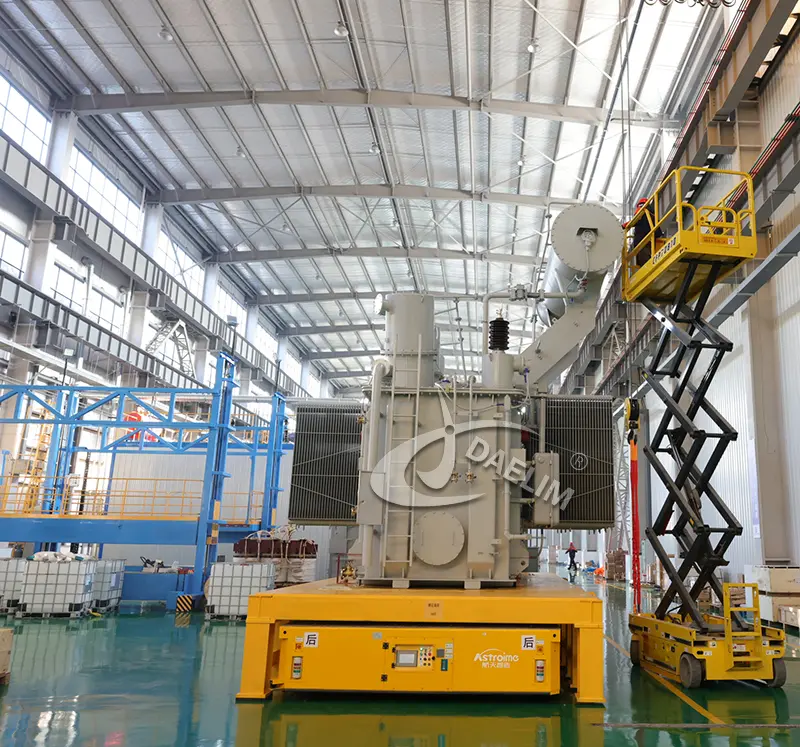
The size, voltage rating, current rating, and capacity of these large power transformers is huge. Their reliable performance is so important that design and manufacturing of these large power transformers requires highly precise and complex manufacturing, assembly, inspection and testing processes.
Material, manufacturing, and testing requirements of each power transformer part are unique and totally depend on their working and performance expectation. So to understand how large power transformers are manufactured, we have to discuss manufacturing of each part individually.
Power Transformer Core Manufacturing
You can say that cores are the centerpiece of transformers and they are responsible for power transfer between primary and secondary transformer winding. As they are considered the core of the transformer and are responsible for transferring power, their quality manufacturing is very important.
They are manufactured using very high quality grain oriented electrical steel. Steel type specially developed for manufacturing of electrical product parts. This steel is used in the form of very thin sheets typically between 0.18 to 0.35 mm. Thin sheets help reduce the eddy current losses during power transfer from primary to secondary winding.
To get the steel sheet of perfect width, the steel coil is sliced into required width using a precision metal cutting machine also called a slitting machine. The machine cut a wider steel sheet coil into a smaller coil of required width. After getting the required width, the steel coil is then processed through a laser cutting machine or CNC punch press to cut the rectangular pieces with high precision.
Several thin sheets of steel will be joined together to make one core but before assembly, each sheet is first coated with an insulation layer of either oxide coating or varnish. This helps reduce eddy current losses and prevent any potential short circuit between core sheets.
After coating, the steel sheets are stacked in a special configuration called step lap configuration. This step lap configuration improves magnetic flux performance of the core and helps reduce core losses. The cores of large power transformers are stacked using automated robots to achieve tight tolerance. The stacked lamination form the E and I shaped core sections.
Stacked sheet if not clamped tightly can be subject to electrical vibration due to high current flow. So the core is compressed using a core clamp or a tie rod to eliminate this electrical vibration. To improve core structure strength a metallic frame made from the same material is used to enclose the sheet. This gives the core more mechanical stability and prevents any movement under the extreme operation load.
As large power transformers are built to last longer without any decrease in their performance. To achieve this, cores of the large power transformer are annealed for stress relieving. Stresses might residual in the steel sheet due mechanical cutting, stacking, and assembling.
You may enjoy: Why Choose Silicon Steel Sheets for Transformer Cores?
Transformer Primary and Secondary Winding Manufacturing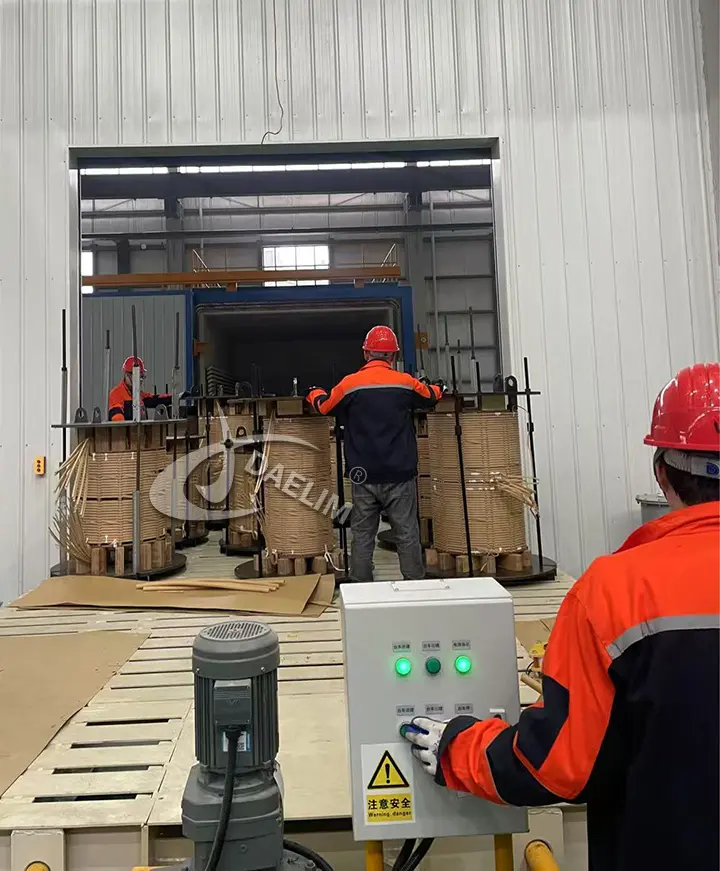
How much electricity your transformer can regulate and whether your transformer is a step up or step down transformer, depends on the primary and secondary transformer winding. Use of high quality material and precise manufacturing process is crucial for manufacturing a high performing transformer winding.
Copper and aluminum are the two most used materials for manufacturing transformer winding and among these two, copper is superior in terms of electrical conductivity with minimal losses while aluminum is a cost effective option. Using copper also means less material will be needed as compared to aluminum to get the same electrical conductive value. Less material means less weight and less space needed for the winding.
As far as the shape of the material is concerned, you can expect both round or rectangular wires for low to medium voltage large power transformers. However for high voltage large power transformers, copper or aluminum foils or strips are used. They are used to reduce eddy current losses.
As there cannot be any direct contact between core and winding and also within different layers of winding. So a proper insulation of the conductor needs to be done. This is also essential to avoid any short circuit in later stages or during the useful life of the transformer.
To insulate all types of electrical wire in the power transformer, special enamel coated wires are used. However in large power transformers oil impregnated kraft paper or Nomex insulation is used to insulate copper or aluminum strips from core. To insulate layers of windings, insulating paper or mylar sheets are placed between winding layers. This insulation ensures dielectric strength remains good between layers and it can withstand high voltages.
The most important process in winding manufacturing is the winding of conducting material itself. The transformer winding is divided into low voltage winding and high voltage winding and both are winded using different winding techniques.
The low voltage windings are made from relatively thicker copper or aluminum strips as they have to handle higher current. The thicker strips can be winded using helical winding technique, disc winding technique or foil winding technique. All three techniques are considered best for large power transformers.
The high voltage windings are made from relatively thinner copper or aluminum strips as they have to handle lower current. The thinner strips can be winded using layer winding technique, continuous disc winding technique or interleaved winding technique.
As windings do most of the electrical power regulating work and all the current that passes through transformers pass through them, you cannot let any moisture present in the winding. To remove all types of moisture, winding is placed and dried in the oven. The oil type transformer winding and core assembly is kept immersed in oil to keep moisture out.
Get it free: Understanding Types of Transformer Winding and Their Applications
Manufacturing of Large Power Transformer Tanks
Large power transformers need a tank to hold their core and winding assembly and the transformer oil that keeps the winding and core assembly immersed. Once everything is installed, the transformer tank is sealed to keep all inside parts isolated from the environment.
The transformer tank has to be made from material that can resist all the environmental factors like wind, trainstorm, and moisture. It also has to resist the heat produced by the transformer winding during the operation.
To enable it to resist all these factors, it is made from high quality steel, usually stainless steel or galvanized steel. Both materials have excellent corrosion resistance and can resist any type of environmental conditions.
The sheet goes through a number of very basic but usually through CNC or automatically controlled precision machines. The steel sheet is first precisely cut into required lengths using a precise cutting process like laser cutting, plasma cutting, and shear cutting machine.
To form the steel sheet into tank-like shape, it is passed through bending and rolling machines that deform its flat shape into tank-like geometry. To complete the tank welding is required and to get the highest strength at all welded joints of the transformer tank,TIG or MIG welding technique is used.
If needed stiffeners are also added in the transformer tank body to give tank extra strengths specially for large power transformers. As the tank is the main body that radiates the transformer heat into the surrounding, the tank might need fins and a cooling system attached to it. Fins depending on the design are either solid fins that are simply welded on the outer side of the tank or are hollow tubes that are welded as a part of the tank. Hollow tubes allow circulation of cooling oil inside them for better heat dissipation.
The transformer tank will take all the external environmental factors and will be subjected to harsh conditions. The outer side of the tank is processed through different surface treatment processes and can be coated with different anti corrosion paints or powder coating.
Reading on: Choosing the Right Transformer Enclosure for Your Project
Challenges in Manufacturing Large Power Transformer
As these transformers are large and manufacturing such a large transformer and that with high precision is a challenge of its own. There are some certain challenges that even the largest power transformer manufacturers in the world might face.
Size and Weight of Transformer
The most obvious of the challenges is the size and weight of the entire large power transformer and also of its individual parts. As each part is made from steel or other metal, it will weigh in hundreds of kilograms if not thousands. Moving, cutting, finishing, and assembling such heavy parts with prevision is a challenge that large power transformer manufacturers in the USA will face.
Try it free: Ultimate Guide To Transformer Sizes and Ratings
Precision Manufacturing Machines
Next challenge that large power transformer manufacturers will face is precision manufacturing machines. These machines are expensive and are so dedicated that they barely do other manufacturing jobs. These are also so sophisticated that operating and maintaining these machines is also a challenge. Initial and operating cost of these machines seriously affect the large power transformer price.
Skilled Workers for Manufacturing
Large power transformer market is huge and with our ever increasing reliance on electricity, it is skyrocketing but there is a serious shortage of skilled workers that understand the procedure and complexity of large power transformer manufacturing. Skill labor shortage is a serious challenge that large power transformer manufacturers USA need to address.
Although the large power transformer market is not influenced much by the large power transformer price , each world economy is in desperate measures to reduce its operation cost. Keeping large power transformer prices low will be a challenge that even the largest power transformer in the world might need to address. Use of a cost effective manufacturing process and development of advanced design can reduce the large power transformer price.
Keep reading: High Voltage Transformer:Definition,Principle,Uses and Price
Environmental Challenges
Large power transformers are so big and they utilize so much material during the manufacturing stage that they can cause contamination of the surrounding environment if not handled properly. They offer the challenge of recycling waste material produced during the manufacturing stage. They also offer the challenge of proper containing and disposing of transformer oil after its useful life. Similarly the insulation material also needs proper disposal after removal from the transformer during maintenance. Use of biodegradable esters for transformer insulation is highly recommended.
Conclusion
Large power transformers are an important part of our electrical power generation system. These electrical machines need to perform exceptionally well in their task of electrical power distribution. To achieve high performance each of their parts needs to be designed, manufactured, tested, and assembled with extreme precision. Use of CNC machines and precision manufacturing machines, and automation or robots to manufacture precise parts is a need but increase the final price of the power transformer. Large power transformers offer challenges of their own and require proper handling to avoid any potential damage to the surrounding environment.
Follow Up
Large power transformers are so large and heavy that manufacturing each part of these transformers and that with precision is a great challenge. Manufacture with transformers is precision and quality that offer high performance needed skills and expertise.
At Daelim Transformer we design, manufacture, assembly, inspect, and test large power transformers. Our transformers are known for their high performance and exceptional reliability around the globe. We are already working in the USA, Canada, Europe, Australia, and other countries where we have successfully operationalized many power transformers.
If you have any questions about large power transformers, Contact Us and we will talk you through the process.
Related Products
Related Article
Conservator Transformers and Their Role in Power System Reliability
Conservator transformers play a critical role in enhancing power system reliability by maintaining optimal oil levels, preventing overheating, and protecting against contamination. The conservator tank stores extra oil, allowing for temperature-related expansion and contraction. It also keeps oil clean by shielding it from air, dust, and moisture. Types of conservators include corrugated, capsule, and diaphragm, each offering unique benefits. Daelim’s conservator transformers, designed to meet international standards, ensure long-lasting efficiency, safety, and reduced maintenance in power systems worldwide.
69 kV Power Transformer for Substation in Pennsylvania
Daelim recently completed the design, supply, and installation of a custom 69 kV transformer for a substation in Pennsylvania. This high-efficiency, three-phase transformer is engineered for reliability, scalability, and long-term performance, ensuring a stable power supply to the substation. Key features include low load losses, minimal maintenance, high insulation levels, and flexible cooling options. The solution enhances grid stability, supports future expansion, and minimizes energy consumption, reinforcing Daelim’s commitment to quality and innovation in power systems.
20MVA Power Transformer for the United States
This project involves the development of a 20 MVA three-phase power transformer tailored for the United States market. The primary voltage is 24.94kV, and the secondary voltage is 4.16kV, indicating it functions as a step-down transformer. The design and production fully comply with IEEE C57.12.00 standards and have passed third-party UL team testing. All accessories also adhere to IEEE standards. FR3 vegetable oil serves as the insulating liquid for the transformers.
230 kV Three Phase Power Transformer For USA Market
In 2023, Daelim Transformer designed and manufactured a cutting-edge 230 kV three-phase power transformer for a client in Nevada, USA. The client recently shared installation and operational photos, showcasing the successful deployment of this remarkable transformer. Let's delve into the specifics of this transformer project!
Canadian 69 kV Substation Transformer Project
Today, we are excited to present a case study on a 69 kV substation transformer project by Daelim Transformer. Our Canadian client required a step-down transformer for their substation to connect with the hydroelectric grid in Quebec.
How To Do Transformer Coil Winding Calculation
Transformer winding calculation involves determining turn ratio, core area, turns per volt, total turns, and wire cross-section. Based on input voltage, current, and frequency, you can design step-up or step-down transformers accurately. Proper wire gauge selection ensures safe and efficient operation. Daelim Transformer offers customized transformer design services to meet specific requirements.