Transformer Temperature Rise: Understand Ratings, Factors, and Impact on Efficiency
Have you ever wondered why transformers get hot during operation? Electrical components, such as transformer windings, generate heat as a by-product, raising the transformer's average temperature.
Efficient transformers are designed to manage temperature rises effectively, unlike less efficient ones. This is a critical consideration when selecting transformers for different applications.
In this article, we’ll explore transformer temperature rise, temperature rating types, considerations for dry-type and oil-type transformers, and temperature charts for effective performance monitoring.
With over 20 years of expertise, Daleim Transformer is dedicated to providing high-performance, reliable transformer solutions for clients worldwide. We specialize in designing and manufacturing oil transformers with temperature rises of 55°C or 65°C, tailored to meet the specific needs of various industries. Whether in industrial, energy, or infrastructure applications, our custom transformers ensure stable operation even in demanding environments and under heavy load conditions. Choose Daleim for outstanding quality and cutting-edge technology that meets all your power needs!
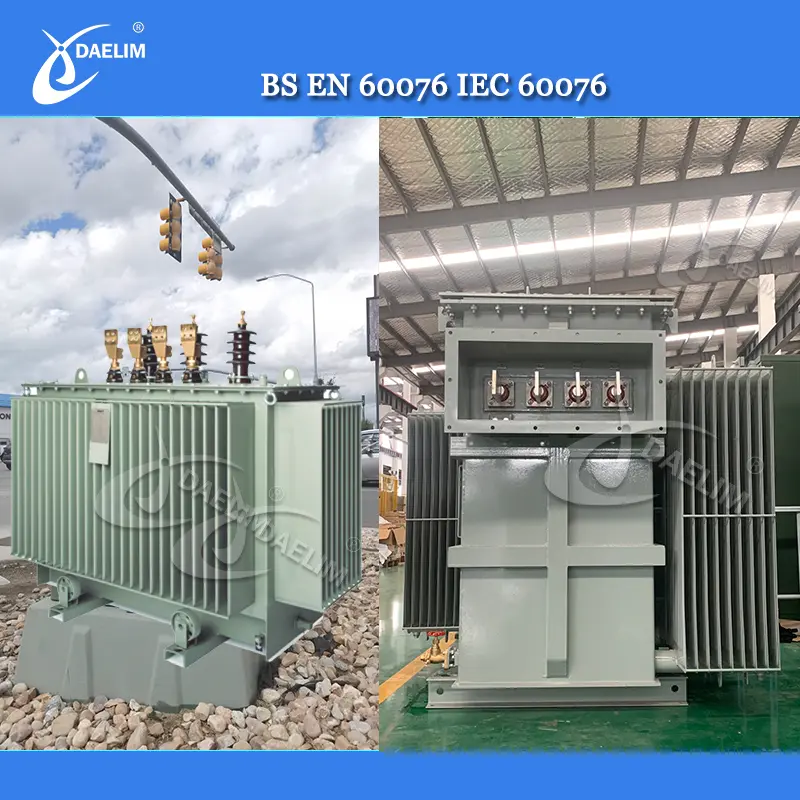
The ECO design transformer (Tier 2) complies with the latest energy efficiency standards of the European Union. Available in both silicon steel core and amorphous alloy core designs, it is engineered for superior energy savings, environmental friendliness, and high efficiency. Designed and produced according to IEC and BS standards, this transformer offers reduced losses and minimized environmental impact. Additionally, the ECO design transformer incorporates advanced temperature rise management, ensuring that the transformer operates within safe thermal limits even under high-load conditions. This feature guarantees enhanced operational reliability, longer service life, and improved overall performance.
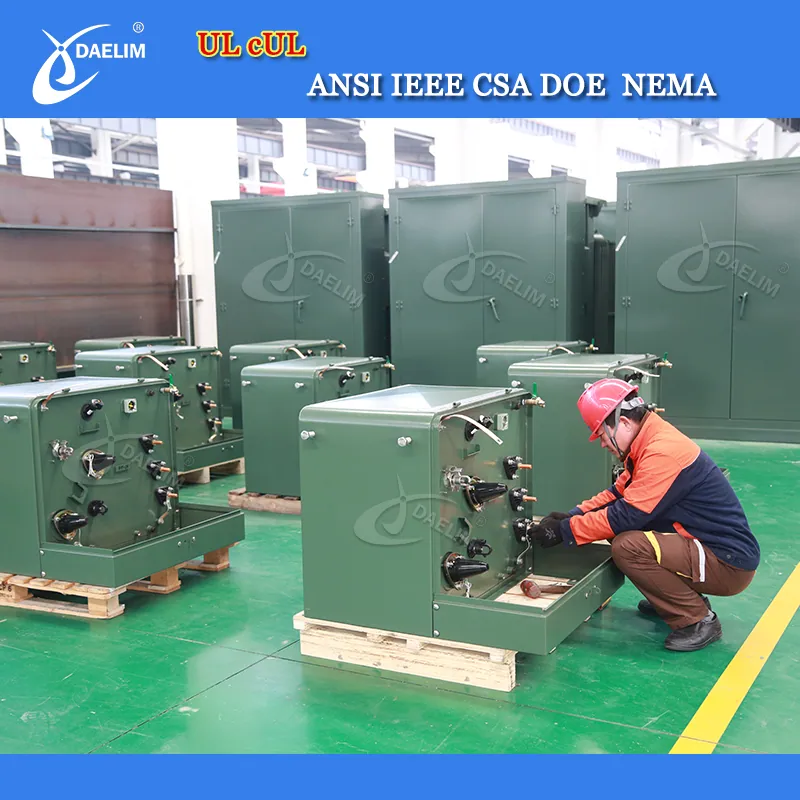
Daelim is a respected manufacturer providing UL/cUL and CSA certified pad-mounted transformers. We offer both single-phase and three-phase options. Our three-phase transformers feature voltages up to 44 kV and power ratings ranging from 75 kVA to 10,000 kVA. For single-phase applications, our pad-mounted transformers support high voltages up to 34.5 kV and ratings up to 250 kVA. All Daelim transformers are designed with advanced cooling systems and carefully engineered to manage temperature rise, ensuring that operational temperatures remain within safe limits for long-term reliability and efficiency. We prioritize performance and safety, providing transformers that meet rigorous temperature rise standards for optimal operation in various environments.
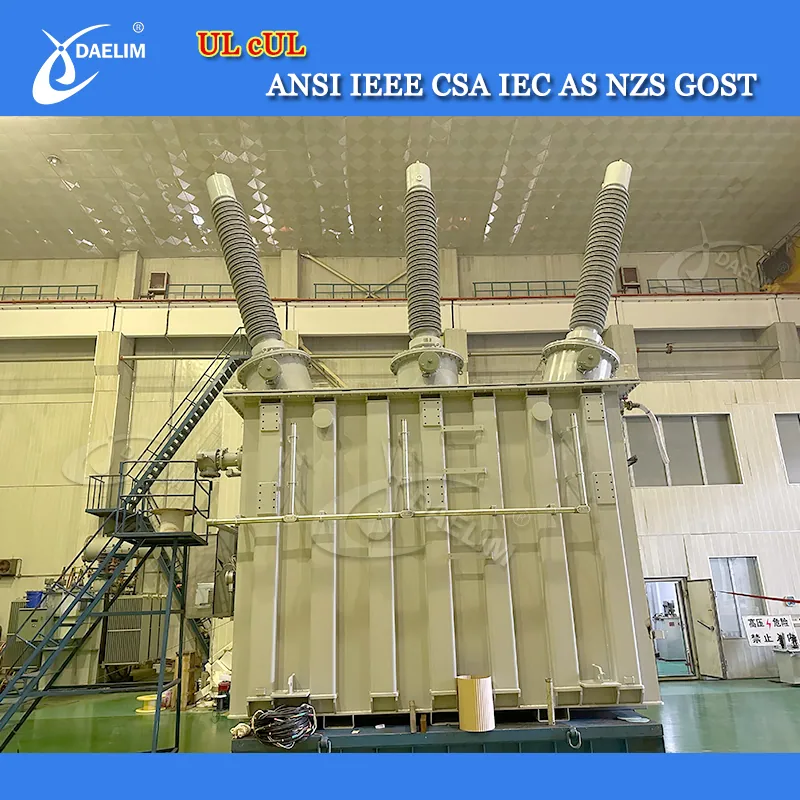
Daelim Transformer offers a complete line of oil-immersed transformers that meet current applicable standards, including IEC, IEEE, ANSI, CSA, NEMA, AS/NZS, and GOST. Our high-voltage power transformers are available for voltages up to 345 kV and ratings up to 500 MVA. Designed for optimal performance, Daelim transformers feature advanced cooling and temperature rise control mechanisms to ensure safe operation under high-load conditions. We have successfully supplied hundreds of high-voltage power transformers across America and Australia, with rigorous testing to maintain temperature rise within the prescribed limits, ensuring long-term reliability and efficiency.
What is Transformer Temperature Rise?
Transformer temperature rise refers to the increase in winding temperature above the surrounding ambient temperature when the transformer operates at its nameplate rating.
Understanding temperature rise is crucial for assessing transformer health, efficiency, and safety, as it indicates how well the transformer manages the heat generated during operation.
Transformers operate based on electromagnetic induction, transferring energy through a magnetic field. However, this process generates heat due to winding resistance and core losses.
International standards such as IEC and ANSI set maximum temperature rise limits—typically 80°C for dry-type transformers and 65°C for oil-immersed transformers—to ensure safe operation.
More resources:
Ultimate Guide To IEEE C57 Standard
CSA C88 Standard For Power Transformers
CSA C802 For Minimum Efficiency Values For Power Transformers
CSA C227.3 For Single Phase Pad Mounted Distribution Transformer
Three Phase Live Front Pad Mounted Transformers Under CSA C227.5
At DAELIM Transformer, we monitor the temperature rise to identify potential overloads or design limitations, ensuring our transformers operate efficiently and safely.
What Causes Temperature Rise in Transformers?
Iron Loss
Inside the transformer core, magnetic flux continuously changes, creating iron losses due to hysteresis and eddy currents, which contribute to core heating.
Copper Loss
As current flows through the coils, the resistance in the coils generates copper losses (often called stray losses), which add to the overall temperature rise.
Poor Cooling
Ineffective cooling systems, whether due to limited coolant flow or poor heat dissipation, can cause the transformer to heat up more rapidly.
Overloading
Operating the transformer beyond its rated load is akin to forcing it to work overtime. This extra current leads to more heat generation and stresses the system.
Ambient Temperature
When the ambient temperature is high, heat dissipation slows, making it harder for the transformer to stay cool, which leads to an increase in its internal temperature.
Understanding Transformer Temperature Rise Ratings
The transformer temperature rise rating (C-rise) is the average temperature increase of its windings, measured in degrees Celsius (°C), above the ambient temperature when operating at full load.
We classify our transformer temperature rise ratings as follows:
Dry-type Transformers
Our dry-type transformers offer three standard temperature rise options: 80°C, 115°C, and 150°C. These values are based on a maximum ambient temperature of 40°C.
For example, a dry-type transformer with an 80°C rise will operate at an average winding temperature of 120°C when fully loaded at 40°C. The insulation on the windings is typically rated at 220°C, regardless of the design temperature rise. As a result, an 80°C rise unit provides more tolerance for occasional overloads compared to a 150°C rise unit, helping to protect the insulation and extend the transformer’s operational life.
Our oil-immersed transformers generally use Class A insulation, which has a maximum allowable temperature of 105°C. The standard temperature rise of the coil is 65°C.
Typically, the transformer temperature is 10°C lower than the winding temperature. Therefore, our allowable temperature rise for transformer oil is 55°C to reduce oil aging.
The transformer will operate safely within its service life as long as the temperature rise stays within the allowable limits, regardless of ambient temperature changes.
Benefits of Transformer Temperature Rise Ratings in Transformer Selection
When selecting your transformer, consider the temperature rise rating (C-rise), as it significantly impacts efficiency, reliability, lifespan, and overload capability:
- Efficiency: Transformers with lower C-rises operate more efficiently, generating less heat and requiring minimal ventilation and cooling.
- Reliability: A cooler-running transformer is more reliable, leading to increased uptime and consistent performance.
- Lifespan: A lower C-rise results in longer transformer life because cooler temperatures extend the durability of internal components.
- Overload Capability: Transformers with lower C-rises can handle a higher overload capacity. For example, an 80°C rise transformer can manage a 15–30% overload without reducing its expected lifespan.
Oil Transformer Winding Temperature Rise
As the voltage increases, the winding temperature of the transformer rises due to both the load and ambient heat. Transformer oil serves as both a coolant and an insulator, absorbing heat from the windings and core and transferring it to the radiators of the transformer
The oil circulates within the transformer: cooler oil from the bottom absorbs heat as it rises, while the hotter oil at the top flows down to complete the cooling cycle.
Factors Affecting Winding Temperature Rise in Oil Transformers
Several factors influence the winding temperature rise of oil transformers:
- Load: Higher load levels increase copper losses, causing the winding temperature to rise. Efficient load management can help minimize excessive heating.
- Cooling System: The cooling system’s performance directly affects temperature. If it malfunctions, the transformer may overheat.
- Insulation: The insulation material and its class determine the temperature rise limits. We use high-quality insulation to ensure optimal temperature management.
- Oil Quality: Moisture in the insulating oil can degrade its electrical and chemical properties, affecting performance.
- Transformer Design: The size and structure of the transformer influence its temperature management. Our engineered designs balance performance and temperature control.
- Power Loss: Resistance in the winding results in power loss and heat generation. We reduce power loss by using quality materials, improving efficiency.
- Iron Losses: Iron losses from core magnetization contribute to temperature rise. We design our transformers to minimize iron losses for better operational stability.
More resource: Losses in Transformer
Dry-Type Transformer Winding Temperature Rise
In dry-type transformers, the temperature rise of the windings is the average temperature increase in °C above the ambient temperature when the transformer is at full load.
DAELIM dry-type transformers rely on circulating air, insulation, and windings for cooling. Overheating can occur when the transformer is handling higher loads and cannot cool down quickly enough.
Key Causes of Temperature Rise in Dry-Type Transformers:
- Inefficient Airflow: Dry-type transformers require adequate airflow and ventilation. Blocked or dusty air inlets and outlets hinder heat dissipation, and obstructions can further restrict it.
- Poor Insulation: Poor-quality insulation can cause overheating and reduced lifespan. Our transformers feature insulation rated up to 220°C to ensure efficiency.
- Low-Quality Windings: Poor-quality windings can degrade the transformer’s dielectric strength and contribute to overheating.
- Incorrect Rating Selection: Selecting a transformer that can’t handle the intended load can lead to overloading and overheating. The load rating indicates the maximum power the transformer can safely handle without risking damage or overheating.
More resource: Comprehensive Guide to Transformer Insulation
Understanding the Transformer Temperature Rise Chart
The transformer temperature rise chart is a useful tool for assessing the efficiency, lifespan, and overload capabilities of our transformers. By conducting a temperature rise test, we can assess temperature increase, total losses, and the final oil temperature rise.
To perform the test, we short-circuit the low-voltage winding, apply voltage to the high-voltage winding, and monitor the top oil temperature hourly. This process helps assess transformer degradation in each phase under load imbalance, provided the oil temperature remains within the maximum limit specified by standards.
Main Components of the Transformer Temperature Rise Chart:
- Insulation Material: The material used for insulation, such as aramid paper or epoxy resin.
- Thermal Class of Insulation: The thermal class of the insulation system, typically classified as A, B, F, H, etc.
- Average Winding Temperature Rise: The average temperature rise of the windings in °C.
- Standard Temperature Rise: The transformer’s standard temperature rise, such as 80°C, 115°C, or 150°C for dry-type transformers.
- Ambient Temperature: The maximum surrounding temperature, typically 40°C.
- Rated Top Oil Temperature Rise: The maximum allowable rise in oil temperature over the ambient temperature.
- Hot Spot Temperature: The temperature at the hottest point within the transformer, which may be higher than the average winding temperature.
Conclusion
In summary, understanding transformer temperature rise is critical for selecting reliable and efficient transformers. Factors such as insulation material, load, cooling system, and ambient temperature all contribute to how well a transformer manages heat. Lower temperature rises result in improved efficiency, greater reliability, and a longer lifespan.
Regular monitoring, along with the use of quality materials and effective cooling systems, ensures optimal transformer performance, preventing overheating and potential damage. By considering temperature rise ratings and relevant factors, you can enhance the performance and longevity of your transformer, ensuring safe and reliable operation for years to come.
If you have any questions about transformer temperature rise or transformer requirements, please contact us
FAQs
What is transformer temperature rise calculation?
Transformer temperature rise calculation involves determining the increase in the temperature of the transformer windings above the surrounding ambient temperature.
How is the transformer temperature rise test performed?
A temperature rise test is conducted by applying a full load to the transformer while monitoring the rise in temperature of the windings and oil
Related Products
Related Article
Everything You Need to Know About Transformer Dimensions
This guide covers the essential dimensions and considerations for selecting, installing, and maintaining transformers. It outlines standard transformer sizes by type and power rating, including medium, high, and ultra-high voltage transformers. Key components like the core, windings, tank, and cooling system are discussed in relation to their dimensions and impact on performance. The article emphasizes the importance of calculating power load, considering location and space, and adhering to industry standards (IEC, ANSI) for safe and efficient transformer operation.
Comprehensive Guide to Unit Substations
Unit substations play a crucial role in safely reducing high voltage from utility lines to levels suitable for use in buildings, factories, and other facilities. They consist of a transformer, primary and secondary distribution equipment, and switchgear. Daelim Transformer provides tailored unit substation solutions, including transformers and switchgear, with extensive experience in the Americas. These substations ensure efficient power distribution, improve safety, and reduce maintenance costs. Contact Daelim Transformer for customized solutions and competitive quotes.
How Long Does It Take To Repair A Transformer?
The time required to repair a transformer depends on factors such as the extent of damage, part availability, accessibility, and the expertise of the repair team. Minor issues like short circuits or blown fuses can often be fixed within an hour, while more complex repairs, such as replacing bushings or pumps, may take several hours or a day. Major faults, like oil leaks or winding damage, could take several days to weeks to fully repair. Timely repairs are also influenced by the accessibility of the site and the experience of the repair team.
Conservator Transformers and Their Role in Power System Reliability
Conservator transformers play a critical role in enhancing power system reliability by maintaining optimal oil levels, preventing overheating, and protecting against contamination. The conservator tank stores extra oil, allowing for temperature-related expansion and contraction. It also keeps oil clean by shielding it from air, dust, and moisture. Types of conservators include corrugated, capsule, and diaphragm, each offering unique benefits. Daelim’s conservator transformers, designed to meet international standards, ensure long-lasting efficiency, safety, and reduced maintenance in power systems worldwide.
Transformer Solutions for Electricity Generation
Daelim Transformer offers tailored solutions for power generation, supporting efficient electricity transmission globally. With expertise in Europe, America, and Australia, Daelim provides high-performance transformers designed for renewable energy integration, large-scale transmission, and remote off-grid areas. Key solutions include step-up transformers, ecodesign transformers, and auxiliary transformers, ensuring minimal energy loss, sustainability, and reliability. Daelim’s transformers meet global standards, offering scalable and customizable options for diverse power generation needs. With proven expertise and global support, Daelim ensures safe, efficient, and reliable power systems for various energy projects worldwide.
Empower Your Data Center with Daelim Transformer
Daelim Transformer provides reliable and efficient transformer solutions for data centers, ensuring high power capacity, safety, and energy efficiency. With customized options such as oil-immersed, dry-type, and smart transformers, Daelim addresses critical needs for redundancy, power quality, and load management. Our transformers offer high reliability, scalable designs, and advanced cooling methods, supporting modern data centers with high-density IT equipment. With ongoing maintenance and monitoring services, Daelim ensures continuous, optimal performance for data centers worldwide. Contact Daelim today to power your data center with confidence.