The Complete Guide to Transformer Oil Dissolved Gas Analysis
DGA is one of the primary ways in which transformer health is monitored by analyzing the gases dissolved in the oil of the transformer. It prevents early detection of faults and failures.
In this guide, we will address the principles of DGA, what DGA says about transformer condition, and how this can be used for making good maintenance decisions.
Why Perform Dissolved Gas Analysis?
Dissolved Gas Analysis (DGA) is one of the most important tools for the maintenance of transformers. Transformers are big machines which help transfer electricity over long distances. However, they may sometimes develop faults or problems.
DGA analysis helps us find out if there are hidden problems inside the transformer by detecting gases in the oil. Small quantities of gases can be formed in the oil when the transformer is in operation.
With this gas monitoring, you will have a problem with the transformer before it completely breaks down. It can save you money, time, and even greater problems like power outages.
Now, let's go over a few of the common problems that DGA can help identify for you. All of these problems produce different gases in the oil; if you know what to look for, you can determine the problem and correct it almost immediately.
Common Transformer Issues and Their Gases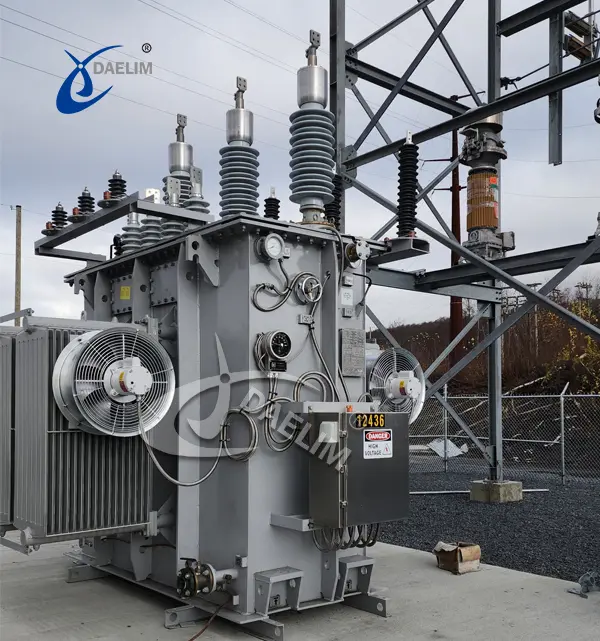
Oil Overheating
This is one of the prominent faults of the transformer. The transformer oil contained within is heated to the breaking temperature point and breaks, and further produces gases, which can possibly have acetylene and methane. That gas appearance is synonymous with the heating of oil within the transformer because of excessive load and less cooling.
Insulation Paper Overheating
Inside the transformer, there is insulation paper which holds everything together inside and keeps away short circuits from electricity. However, when the transformer gets red-hot, this paper can catch fire.
When this happens, carbon monoxide, carbon dioxide, and acetic acid gases are released. That means the insulation paper is being damaged and you should take notice of the transformer.
Due to DGA, this fault can be detected early and avoids further damage to the transformer.
More resource
Transformer Insulation Failure
Air Ingress
Ingress of air refers to that condition when air gets inside the transformer; that is a serious affair. When oil and air mix, they produce gases like oxygen and nitrogen.
This might bring on oxidation as well as even more rapid oil oxidation. Should oxygen continue coming in through the transformer, it would cause the oil along with, of course the transformer to degrade.
This will enable DGA to track the entry points of the air leaks so that these points can be sealed even before they become issues.
Partial Discharge
Partial discharge is an event wherein electrical sparks show up within the transformer. This can be due to damage in the insulation. These small sparks produce hydrogen gas and carbon monoxide gases.
If you ever see them in the oil then a partial discharge occurs; partial discharge increases in size to more extensive electrical-related problems or even transformer failure unless stopped.
DGA gases analysis helps in early detection of this condition, therefore action is taken towards rectification of the issue before it becomes a major problem. All these issues can be caught before they cause critical damage to your transformer when you perform DGA.
The gases in the oil tell you a lot of what is happening inside your transformer, and DGA gives you the tools to understand them; hence, you keep on running your transformer smoothly with no expensive repairs or replacements.
The DGA Testing Process
DGA is one of the most important tests, which lets you see the condition of your transformer. It involves observing dissolved gases in the oil contained within your transformer. Therefore, dissolved gases could explain if something was amiss inside the transformer.
The DGA testing multi-step process assures the sample of oil is clean and safe to test. Let's go through each step so that you may understand how the process goes and why it's so important to keep your transformer in good condition.
More resource
How to analysis of gases and check oil level in transformer?
Step 1: Release Oil Tank Pressure
First, pressure inside the oil container of a transformer is released. Transformers are sealed under pressure so that the trapped oil and gases inside the tank are kept to certain levels.
Before you take a sample, you must bleed some of the pressure carefully so that it is safe to open the valve. This is because it prevents oil spilling or splashing and keeps everything safe for the person doing the test.
Hence, the safety precautionary measures should be taken properly as well as pressure must slowly and safely be released.
Step 2: Clean the Drain Valve and Hose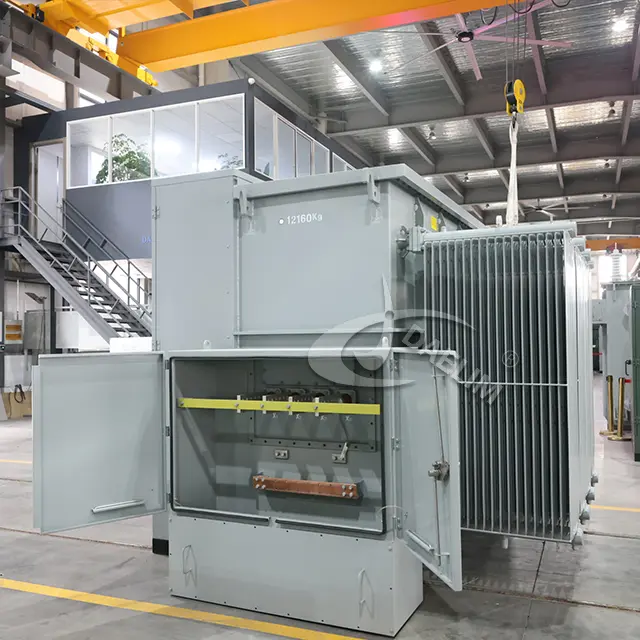
Ensure the drain valve and the hose are cleaned after safely removing the pressure as the valve would have sucked the oil sample from it and should thus be clean of contamination.
Cleaning the valve and hose will ensure that no dirt and dust, or old oil, goes into the new oil sample. In case the sample is contaminated, the test results may come out not accurate and miss an important issue to this transformer.
Cleaning this equipment also makes the whole testing process safe and accurate.
Step 3: Draw the Oil Sample
Once the valve and hose are cleaned, take your oil sample. Sampling a small amount of oil from the transformer for testing involves it.
This is where you get an idea of how the condition of the dissolved gases in oil is of what condition the transformer is. You have to take the oil sample very carefully to see whether it reflects the inside situation of the transformer or not.
This is because the sample will tell you much about what is happening inside the transformer, and you want to be sure that you get a good sample.
Step 4: Remove Air and Prepare the Sample
Draw an oil sample then remove the air trapped inside the sample. Air has a negative impact on the outcome of the test, hence the need to ensure that it is air-free.
Once the air in the container is evacuated, the sample is ready to be placed into testing. The clean container seals it tight, which keeps the oil sample safe from contamination.
It is ready to take into the laboratory for analysis and identifying the dissolved gases in oil, and from the results obtained from those gases, there could be a problem or issue in the transformer.
Step 5: Dispose of Waste Oil and Repressurize the Transformer
After taking and preparing the oil sample, the final step is the removal of the waste oil; you are not allowed to dispose of the used oil somewhere else since it is harmful to the environment.
Check with local regulations for proper disposal of the oil. Once it has been disposed of, pressurize the transformer to put it back into normal service. This means that the transformer has been adequately served with proper and safe working operation.
By following the five steps above, it is possible to carry out DGA testing on the transformer and get accurate information about the health of your transformer. This process is quite critical in catching problems early on to prevent transformer breakdowns.
More resource
How to test a power transformer?
Benefits of Regular DGA Testing
Regular Dissolved Gas Analysis testing is important for the appropriate care of the transformer. As discussed above, a transformer is responsible for passing the electricity from one area to the other. If something happens with it, then it is something big that might arise; otherwise, the supply is zero.
It also helps detect issues early on and saves you money in the long run, all while keeping everything in running order. Let's now discuss a few benefits of doing DGA testing regularly.
Early Detection of Problems
Some of the significant benefits of scheduled DGA testing are that this can easily help you diagnose problems earlier. Once problems start appearing in a transformer, be it overheating or the damage to the insulation within it, several types of gases evolve in the oil.
DGA testing checks for these gases, and if there is a problem, the gases will show it. For example, in case of overheating in a transformer, gases such as acetylene may form.
Regular tests will detect those gases early, and the problem may therefore be corrected before it happens to cause a major failure. Early detection of problems means a lesser chance of expensive repair jobs or long periods of downtime.
Prolongs the Life of Your Transformer
The proper DGA testing prolongs a transformer's life. Like other machineries, a transformer must be serviced periodically for the continuous continuation of its work.
Perform DGA testing to find small problems that may otherwise not be noticed but can develop into bigger ones with time. The transformer lasts longer and performs better when small problems are nipped in the bud.
This will enable monitoring the health of a transformer on a daily basis, thus avoiding expensive replacement and thus ensuring it lasts for long.
Prevents Unexpected Breakdowns
Sudden breakdowns are among the worst problems related to it. The transmitters of electricity in the system are probably its most important pieces; therefore, a transformer that is suddenly failing can cause much trouble in the total system power.
Regular DGA testing will keep the above type of shock breakdowns away. Gases in oil inform in advance about any thing gone wrong and one can act in time before the transformer breaks down.
It, of course, means fewer surprises, less chance of experiencing it in the dead of night or while you're away on an ill-prevented vacation. Knowing your transformer is in good shape keeps the peace and helps everything to just run smoothly.
Saves Money on Repairs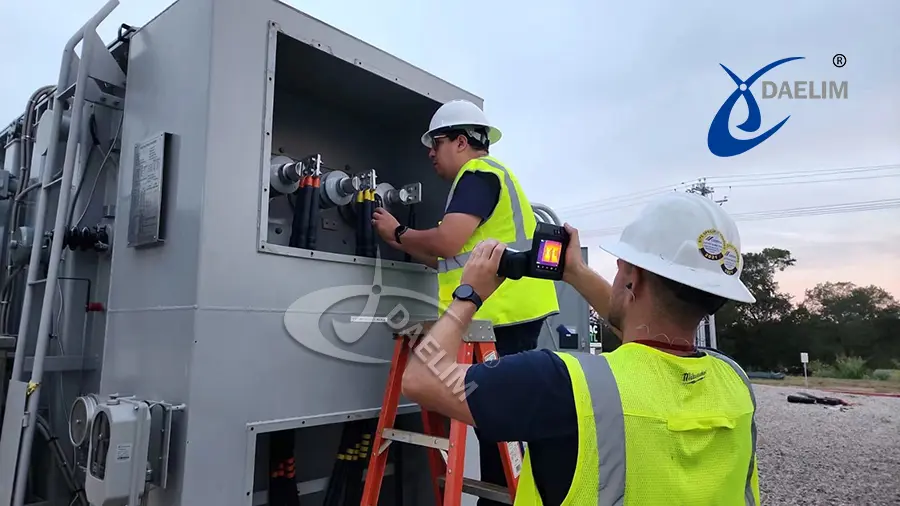
Transformers are just so expensive as things to replace or maintain; the cost of large failures is really quite an expensive investment. Regular DGA testing helps you solve the problem early, allowing small problems to be identified before they become expensive maintenance work.
For example, you notice that oil temperature starts increasing or insulation is beginning to deteriorate at a point where you might shut down before things get a whole lot worse and expensive. You might solve your problem before significant spendings so as not to face huge, big money repair costs, at times maybe even averting having to replace the transformer.
More resource
How Long Does It Take To Repair A Transformer?
Helps Plan for Maintenance
Regular DGA testing also helps you in planning. Knowing what is happening inside your transformer helps in planning the routine maintenance and repairs.
DGA testing can actually give you an insight to which parts of the transformer need attention, hence repaired before they cause trouble. Such planning helps in easier timing in taking the transformer offline for necessary maintenance, hence not hitting any unexpected interruptions.
This can also be planned for parts that are required to be replaced or fixed before they fail completely, and your transformer will always work at its best.
Provides Valuable Data
Regular DGA testing provides you with valuable information regarding the condition of your transformer. Every test will provide you with data about the gases in the oil and what is happening with your transformer.
In due course, you will see when the patterns and trends may appear so that you might forecast when the problems may arrive. Again, it's really worthwhile information as well, for it presents a clearer view on the health of your transformer so you may better have decisions about its maintenance and repair.
Tips for Accurate DGA Testing
DGA testing is one of the most important methods for checking on how your transformer is working. Therefore, if you do this test well, you will get good results.
The following can assist you in drawing out the best from your DGA testing so that you take good care of your transformer and ensure it is working correctly.
1. Always Follow Safety Procedures
All precautionary measures should precede any DGA test. This includes the use of personal protective equipment, for example, gloves and goggles.
Transformers are accident-prone. Be prepared in terms of safety beforehand. If you do not know how to handle all equipment properly, then request some expert's assistance and ask the guidelines about handling and operating such equipment that do not allow accidents.
2. Make Sure the Transformer is Cool
Before you draw an oil sample, cool the transformer if it has been in operation. Hot oil can give skewed results; thus, may lead to some wrong conclusions based on its performance.
When the oil becomes too hot, the gases which may mix in an entirely different manner cause those results to be unreliable. Wait until it cools down to an appreciable temperature before undertaking any DGA test because a warm transformer is really hazardous to work with.
3. Clean the Equipment Before Testing
All components must be clean during a DGA test. Dust, dirt, or old oil may influence the outcome accuracy.
Clean the drain valve, hose, and all the tools before taking a sample of the oil. This avoids the influence of dirt on the test so that you can assure yourself about the accuracy of the test result. A clean sample is very important to ensure proper test results.
4. Use the Right Sampling Method
You need to sample the oil in the proper manner if you want the best results from DGA. It must be sampled from the center of the oil tank rather than from the top or the bottom.
This will give you a sample representing all the oil within the transformer. It is wrong taking a sample from just one portion of the tank as that may not show what's really going on inside.
5. Take the Sample at the Right Time
The time required to conduct DGA tests is very crucial. If it is carried out immediately after the transformer has been turned on or off, probably the gas levels may be high, and hence it may lead to a false test.
Get the best result when you take a sample after the transformer has been running for quite some time in steady mode. This will allow you to understand the building gases that take time to be noticed and thus help in the possible detection of early problems.
6. Make Sure the Oil Sample is Well-Mixed
Stir the oil sample a little once taken, so that gases dissolved in it are equally distributed, then you should take it to the lab for analysis.
This may also mean that some of the gases can be left behind, hence leaving you incomplete information about the inside scenario of the transformer. Mixing this sample before its dispatch means you will receive more accurate results.
7. Use a Certified Lab for Analysis
After you collect and prepare your oil sample, send it to a laboratory qualified to perform this test. Be sure that the laboratory you select is experienced in DGA testing using reliable equipment.
A credible lab gives you results you can depend on. Using a good lab will ensure you obtain the right information to care for your transformer.
8. Record All the Details
All details of the test must be written down during DGA testing. This includes the date and time the test was carried out, the oil's temperature, equipment used, and other important notes.
Good records will trace out how the transformer's health will evolve with time and changes are easily noted or understood. It also helps to maintain organization and provides a reference guide to compare test results later on.
9. Repeat Testing Regularly
DGA testing isn't done once. You will have to take regular DGA tests if you want to keep track of the health of your transformer.Testing often helps you find the problems early and ensures the transformer is always in good condition.
The frequency of testing may differ with the amount of usage that the transformer has, but a minimum of once a year, it's a very smart choice to test the transformer. With regular tests, you can be sure the transformer is safe and doing well.
10. Take Action Based on the Results
The day you receive the DGA test result, you should understand what it says and do something if required. If there are bad gases inside the oil, then something is inside the transformer that needs fixing. You will easily tell whether maintenance or repair is required if you understand what results mean.
If you are not sure, seeking expert advice, such as from Daelim Transformer, can help you take the right steps to keep your transformer working well. For over 20 years, we have worked with Fortune 500 companies and solved their different issues in their transformers.
We also hold multiple certifications including ISO 9001:2008, UL/CUL Certification, CSA Certification, CESI Certification, and CNAS Certification.
Conclusion
DGA testing is very essential to check how well the transformers are working. Knowing the results and doing the right thing will help you stop the problems before they arise. Need assistance? Contact us today!
Related Products
Related Article
Conservator Transformers and Their Role in Power System Reliability
Conservator transformers play a critical role in enhancing power system reliability by maintaining optimal oil levels, preventing overheating, and protecting against contamination. The conservator tank stores extra oil, allowing for temperature-related expansion and contraction. It also keeps oil clean by shielding it from air, dust, and moisture. Types of conservators include corrugated, capsule, and diaphragm, each offering unique benefits. Daelim’s conservator transformers, designed to meet international standards, ensure long-lasting efficiency, safety, and reduced maintenance in power systems worldwide.
Transformer Solutions for Electricity Generation
Daelim Transformer offers tailored solutions for power generation, supporting efficient electricity transmission globally. With expertise in Europe, America, and Australia, Daelim provides high-performance transformers designed for renewable energy integration, large-scale transmission, and remote off-grid areas. Key solutions include step-up transformers, ecodesign transformers, and auxiliary transformers, ensuring minimal energy loss, sustainability, and reliability. Daelim’s transformers meet global standards, offering scalable and customizable options for diverse power generation needs. With proven expertise and global support, Daelim ensures safe, efficient, and reliable power systems for various energy projects worldwide.
Empower Your Data Center with Daelim Transformer
Daelim Transformer provides reliable and efficient transformer solutions for data centers, ensuring high power capacity, safety, and energy efficiency. With customized options such as oil-immersed, dry-type, and smart transformers, Daelim addresses critical needs for redundancy, power quality, and load management. Our transformers offer high reliability, scalable designs, and advanced cooling methods, supporting modern data centers with high-density IT equipment. With ongoing maintenance and monitoring services, Daelim ensures continuous, optimal performance for data centers worldwide. Contact Daelim today to power your data center with confidence.
Transformer Temperature Rise: Understand Ratings, Factors, and Impact on Efficiency
Transformer temperature rise refers to the increase in winding temperature above the ambient temperature when a transformer operates at full load. It is influenced by factors like iron loss, copper loss, poor cooling, overloading, and ambient temperature. Transformers are rated with specific temperature rise limits (e.g., 65°C for oil-immersed and 80°C for dry-type), which impact efficiency, reliability, lifespan, and overload capacity. Proper monitoring and high-quality materials ensure safe, efficient operation, preventing overheating and extending transformer life.
69 kV Power Transformer for Substation in Pennsylvania
Daelim recently completed the design, supply, and installation of a custom 69 kV transformer for a substation in Pennsylvania. This high-efficiency, three-phase transformer is engineered for reliability, scalability, and long-term performance, ensuring a stable power supply to the substation. Key features include low load losses, minimal maintenance, high insulation levels, and flexible cooling options. The solution enhances grid stability, supports future expansion, and minimizes energy consumption, reinforcing Daelim’s commitment to quality and innovation in power systems.
Signs That You Need to Replace Your Oil-Filled Transformer
This article discusses the key indicators that signal the need for replacing an oil-filled transformer, including persistent oil leaks, abnormal infrared scan results, unusual vibrations or noises, and poor DGA test results. It emphasizes the importance of recognizing these signs early to prevent downtime, efficiency loss, and environmental damage. Additionally, the article highlights the impact of aging transformers and rising energy costs, recommending timely replacement to ensure optimal performance and compliance with modern standards