How Transformer Components Function Together to Control & Deliver Electricity
Electrical Transformers are responsible for controlling and delivering electricity between your local grid station and home or factory. Each transformer component is designed, manufactured and assembled for optimal power regulation. There are more than 14 different transformer components and we will discuss them in detail here.
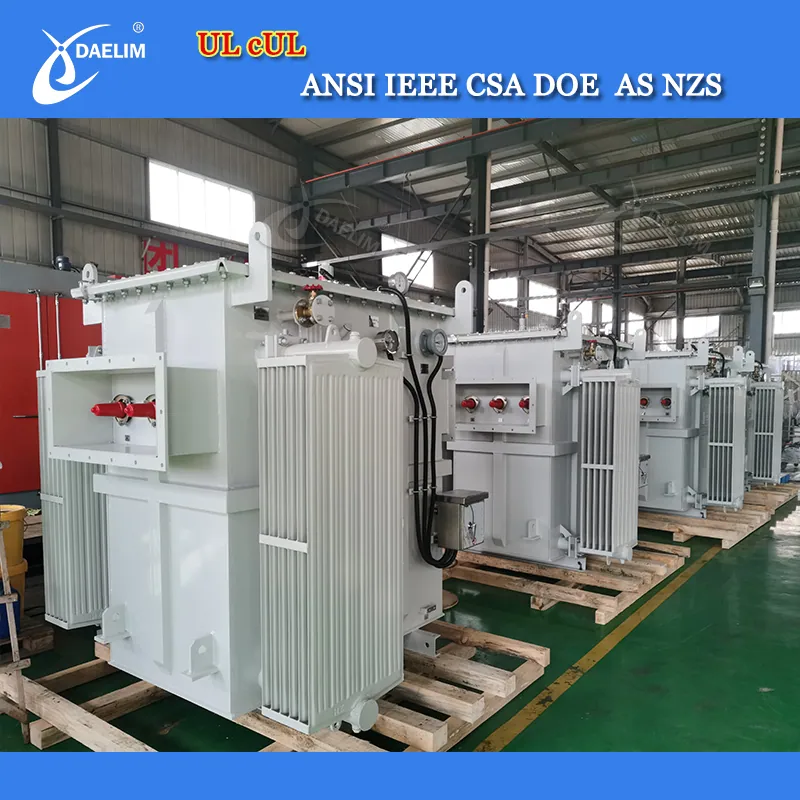
Daelim Transformer's three-phase substation transformers are designed for high voltages up to 44 kV and ratings of up to 20 MVA, compliant with global standards such as ANSI/IEEE C57, CSA C88, IEC 60076, and AS. These transformers are equipped with monitoring system accessories and feature components from internationally renowned brands like ABB, Copper, and Qualitrol.
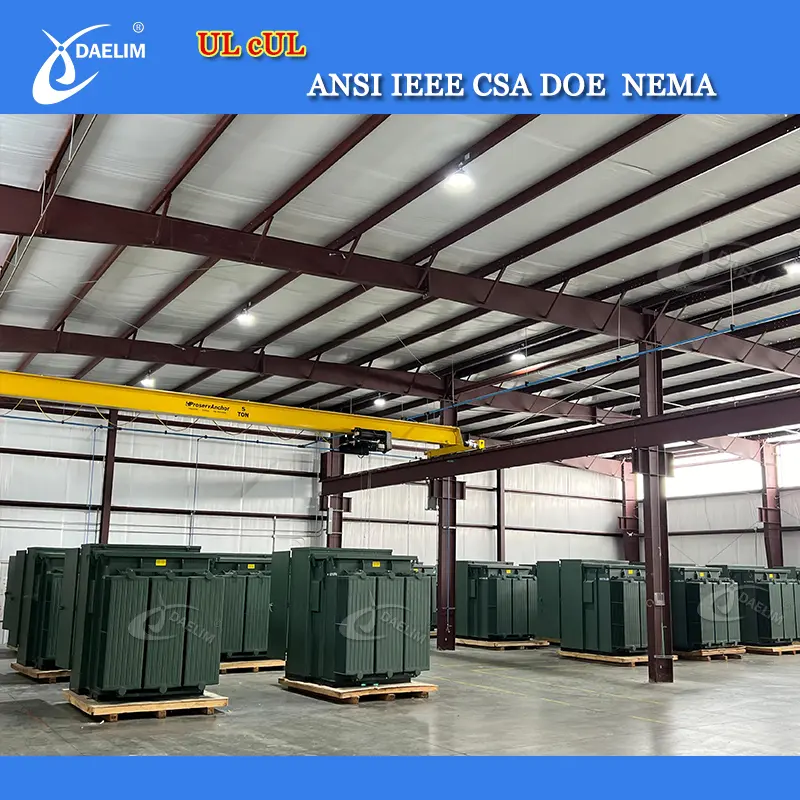
At our facility in Houston, we have hundreds of transformers in stock, including pad-mounted transformers ranging from 300 kVA to 3000 kVA, with voltage levels of 12.47, 13.2, 13.8, 24.94, and 34.5 kV. We also offer single-phase transformers with capacities from 50 to 175 kVA. There's no need to wait—immediate shipment is available!
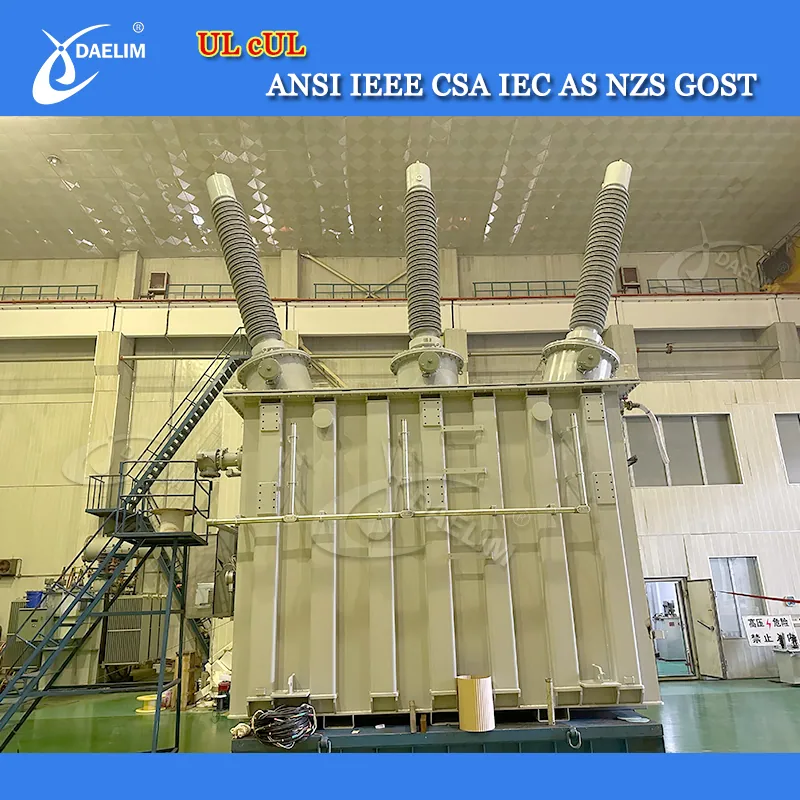
Daelim Transformer offers a complete line of oil-immersed transformers that meet current applicable standards, including IEC, IEEE, ANSI, CSA, NEMA, AS/NZS, and GOST. Our high-voltage power transformers are available for voltages up to 230 kV and ratings up to 300 MVA. We have successfully supplied hundreds of high-voltage power transformers across America.
How Different Transformer Components Function Together in Oil Type Transformer
Transformer Winding
Transformer winding is a metal wire that has been turned multiple times and bundled together onto a part of transformer called core. Winding wire is usually made of copper for high quality transformers due to copper's excellent electrical conductivity and ductility. Winding can also be made of aluminum for cost effectiveness but at compromised performance.
There are two different windings in an Electric transformer, a primary winding and a secondary winding. Primary winding is connected to your local grid station supply and secondary winding is connected to your home or factory input.
In single phase transformers, there is one primary and one secondary winding. In three phase transformers, there are three primary and three secondary windings.
Main function of transformer winding is to take electrical voltage and current from your local grid station and transfer it to your home in a controlled manner. Winding controls the voltage and current through the number of turns of the wire made on the core. Number of turns is controlled by the tap charger.
In step-up configuration, the number of turns of primary winding is less than that of the secondary winding. In step-down configuration, the number of turns of primary winding is more than that of secondary winding.
In step-up configuration transformers increase the incoming voltage. In step-down configuration it reduces the incoming voltage and delivers it to your home.
Transformer Core
Transformer core is a metal frame onto which the transformer winding wire is turned and stacked on. Transformer core is made of soft metal / ferrous metal like silicon steel. The reason why it is made from soft metal is what the core does.
Main function of the core is to provide an easy path to the magnetic flux developed at the winding. This helps an efficient non-contact connection between primary and secondary winding.
The soft metal provides a low resistance path for magnetic flux by helping reduce eddy current losses. It also holds the flux within the transformer body. Primary winding is done on one side of the core while the secondary winding is done on exactly opposite side of the core where primary winding has been done.
The core of a single phase transformer is simpler as compared to the core of the three phase transformer. Core of the three is designed to enable stacking of three different primary and three different secondary windings, therefore it is more complex than a single phase transformer core.
Insulating Material
As transformer winding and core are both made of metal, their direct connection will short circuit the entire transformer. To prevent this, an insulating material like special paper or a cardboard is used to establish non-contact assembly of winding and core.
There is an insulating material between winding and core to avoid direct connection. There is also another layer of insulating material on top of the winding surface. This is to avoid any unintentional connection between primary and secondary winding or any other part of the power transformer.
All other connections are also insulated by either using insulated wires for connection or using special insulations. This is done to prevent short circuits within the transformer components and for safe control and transfer of electrical power.
Transformer oil
The working mechanism of the transformer is such that it generates a lot of waste heat. Regulation of electric current and voltage at the primary and secondary winding is the main reason behind this heat. This waste heats so much that it can damage any or all components that are not protected against it.
So to protect components and to transfer and waste heat from winding into the outer environment, transformers use oil. It's also called the cooling fluid and in some cases lubricant. The oil has a high coefficient of thermal conductivity. So it very easily and quickly absorbs heat from winding and transfers it to the transformer body. Body then radiates that heat into the surrounding atmosphere.
Transformer Tank
All important transformer parts like winding and core are placed inside a secure tank called a transformer tank. Tank is usually made from high quality steel that is surface treated to increase its resistance against corrosion and other environmental factors. The primary purpose of this tank is to seal and isolate the transformer components from the external environment.
The tank not only isolates winding and core, it also provides space and acts like a pan for the transformer oil. The tank also acts like a base for all other electrical transformer parts like conservator, cooling tubes, and breathers.
Cooling Tubes
As we have mentioned above, the transformer working principle produces a lot of heat. The transformer oil is responsible for removing that heat from winding and transferring it to the outer atmosphere. Now if the heat produced by the transformer is of such intensity that oil cannot remove it efficiently.
Then a design feature called cooling tubes is added to the transformer body. These are hollow tubes integrated into the transformer tank. The oil in the tank is moved through these tubes using a pump.
These tubes provide greater area for heat transfer from oil to tube body and then from tube body to outer atmosphere. Due to which, now oil can quickly and efficiently transfer heat from winding to outer atmosphere
Transformer Conservator
The transformer oil like every other material on earth expands on heating and contracts on cooling. So as the load on transformer winding increases, they generate more heat. As a result the oil heats up more than usual and expands.
In order to control this expansion and contraction of oil and provide oil enough space to move, a special container is used called a conservator. It's a cylindrical tank attached to the main tank of the transformer via a tube.
Conservator is kept half empty to compensate for the inflow of oil. The conservator is installed on the main tank in such a way that it keeps the main tank full of oil. This makes the system safe and enables the transformer proper dissipation of heat.
Transformer Breather
In a transformer when oil expands due to heat, it pushes the air present in the transformer conservator out. Similarly when it cools, it sucks in air as it moves back from the conservator into the main tank.
Transformer breather is a specially designed air inlet for the transformers. It is attached with the transformer conservator and it is the only place from where air can enter the transformer. The main function of the transformer breather is to take in the air and remove all of its moisture before allowing it to enter the conservator.
To remove moisture from fresh air, silica gel is used. It completely fills the breather and air can only enter the conservator after passing through the silica gel. Gel completely absorbs moisture and only dry air enters the transformer. This helps prevent the transformer from any type of rusting and other environmental damages caused by moist air.
Transformer Explosion Vent
During the day to day working of transformers, there might be an event that can lead to transformer components malfunctioning. This malfunctioning can produce extra heat and can make the transformer oil boil.
This boiling oil can establish such a pressure inside the transformer tank that it can explode. To prevent this, a small safety hole is made on the top of the transformer conservator. This safety hole allows easy release of pressure by allowing the boiling oil to exit the transformer conservator.
This is usually a one way valve and oil can only exit the conservator through it and nothing can enter the conservator through this safety hole.
Transformer Buchholz Relay
Transformer buchholz relay is a safety component. It monitors the gasses that might be produced inside the transformer due to malfunctioning wires of transformer winding. This relay is installed on the pipe that connects the transformer conservator and transformer tank.
Tap Charger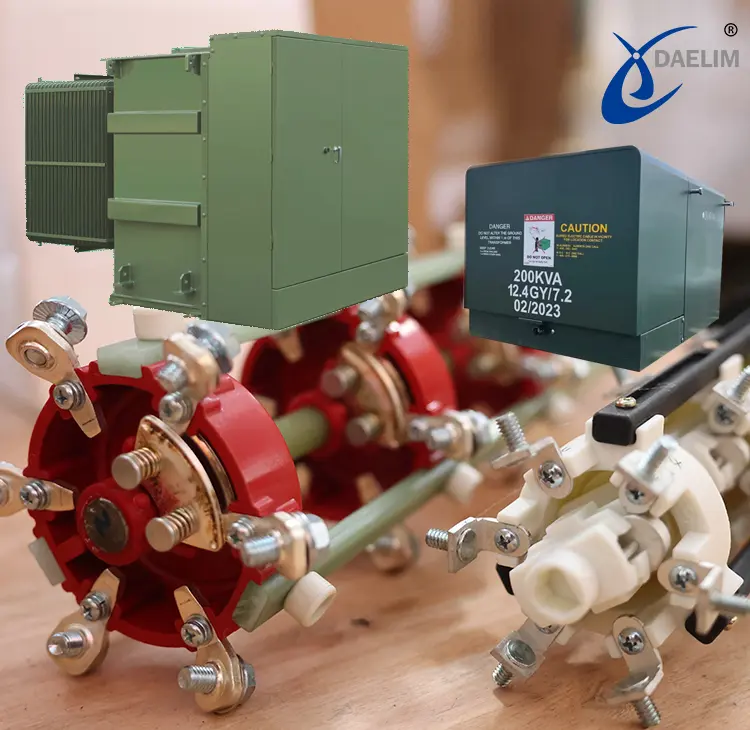
Tap charger is an important part of the transformer. It is used to increase or decrease the number of turns of transformer winding, thus controlling the voltage regulation of the transformer.
There are two main types of tap charger. One is an on-load tap charger that can increase or decrease the number of turns of winding without disconnecting the transformer from the main grid station.
Another is an no-load tap charger that can only change the number of turns of winding when the transformer is disconnected from the grid station and no power is being supplied to the transformer.
Transformer Terminals
Transformer terminals are the connecting points of a transformer. It is these points from where the transformer windings both primary and secondary are connected to grid station and local installation respectively.
One end of these terminals is connected to the transformer winding and is not visible from outside. The other end of these terminals is easily visible outside on the top of the transformer. These terminal ends are specifically designed to facilitate the easy and safe installation of electric circuits using the power lines coming from your local grid station.
Reading more: Guide to Types of High-Voltage Bushings for Pad-Mounted Transformers
Guide to Types of Low-Voltage Bushings for Pad-Mounted Transformers
Dry Type Transformer Components
Dry type transformers are those transformers that do not rely or have oil surrounding their winding for cooling and isolation purposes. Working principle of these transformers is exactly the same as oil type standard transformers but they have fewer components as compared to oil type transformers.
Dry type transformer does not have oil, so no need for a conservator explosion vent, cooling tubes, and breathers. To compensate for these parts and to do necessary cooling of the winding and core, dry type transformers have following parts in addition to standard parts of a transformer.
Winding of oil type transformers is isolated and protected from moisture by use of oil. Same thing in dry type transformers is done using insulating materials like epoxy or polyester varnish.
These chemicals when applied on the winding developed as a strong heat resistant layer of material over the winding. This layer completely isolates the winding from the outer environment thus protecting it from moisture.
Cooling Fan
To remove heat, a standard transformer uses oil but in dry type transformers, a cooling fan is used. Fans take fresh air from one side of the transformer tank and blow it on insulated winding with force.
This produces a force convection phenomena of heat transfer that in return cools down the transformer winding. As windings are insulated so there is no problem of moisture in the air being blown on winding.
Conclusion
In conclusion, transformer components work in perfect harmony to regulate & deliver electricity effectively to your home. Key parts of the transformer such as the winding, core, insulating materials, and oil play crucial roles in ensuring smooth energy transfer between grid station and your home.
The winding transfers voltage and current, the core provides a magnetic flux path and the oil helps in dissipating heat generated during operation.
Additional elements like the transformer tank, conservator, cooling tubes, and tap charger further support efficient functioning, while safety features such as the breather and explosion vent prevent damage.
Each component is integral to ensuring optimal transformer performance and safe electricity delivery.
Whats Next
We hope this article has provided valuable insights about how transformer components function together to regulate and deliver electricity. At DAELIM Transformer, We commit to being your go to resource for all your transformer related needs.
Whether you're looking to enhance your understanding of transformers, or require assistance in selecting the right product our team is here to help.
With a wide range of transformers available for quick delivery. We can meet your project specific requirements. Contact us today to speak with one of our experts and explore more articles to deepen your knowledge of transformer systems.
Related Products
Related Article
What Happens When A Transformer Blows?
Transformers are crucial for our electrical infrastructure, but when they fail, the consequences can be severe. A blown transformer can lead to power outages, fire hazards, and damage to property and electrical devices. Understanding the causes and impacts of transformer failures is essential for ensuring safety and reliability. At Daelim Transformer, we prioritize quality and innovation to minimize these risks.
What Is An OLTC Transformer and How Does It Work?
Are sudden voltage drops affecting your industrial operations? Your aging transformers may struggle to meet energy demands. Fortunately, Daelim's On-Load Tap Changer (OLTC) transformers offer a solution. These advanced devices allow for seamless voltage adjustments without interrupting power, ensuring stability and efficiency. Discover how OLTC transformers can enhance your energy management and protect your equipment in our comprehensive guide.
What Is An NLTC Transformer and How Does It Work?
An NLTC (No Load Tap Changer) transformer efficiently adjusts voltage levels while de-energized, ensuring stable power supply in manufacturing and industrial applications. By manually changing the transformer’s turn ratio, NLTCs maintain optimal voltage without interrupting operations. Their simplicity, reliability, and cost-effectiveness make them ideal for systems with infrequent voltage adjustments. Discover Daelim's NLTC transformers for enhanced energy efficiency.
How to Choose Transformer Supplier
Choosing the right transformer supplier is crucial for ensuring stable power supply and efficient operations. Start by identifying your specific transformer needs, researching potential suppliers, and evaluating their quality and reputation. Consider pricing, customer support, and delivery logistics. Ultimately, trust your instincts and maintain open communication to establish a strong partnership. Discover reliable solutions with Daelim for optimal energy usage.
A Guide to Tier 2 Transformers
This article discusses the EU's Tier 2 Ecodesign Regulations aimed at reducing transformer energy losses. By enhancing design and materials, these regulations lower CO2 emissions and operating costs. DAELIM Transformer is highlighted as a leader in producing compliant, high-efficiency transformers that support sustainability and improved energy performance.