What is Transformer Cooling and How is it done?
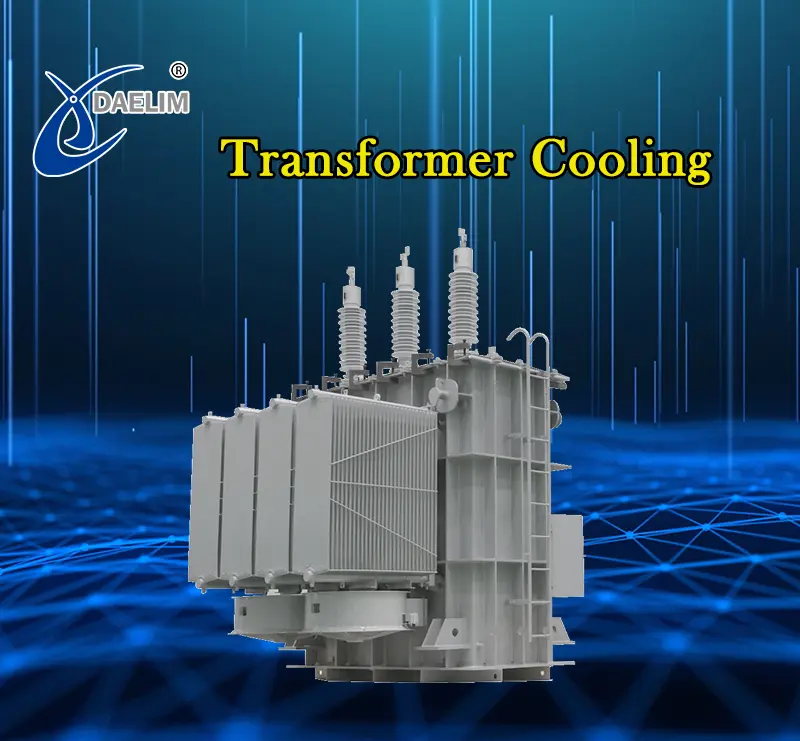
Electrical transformers you see are designed and developed to regulate MegaWatts of electricity. They do regulate electricity with quite an efficiency but with one drawback. They produce a lot of waste heat as they step down or step up electricity for our safe use. With this the concept of transformer cooling started but why cooling of transformers necessary?
Electric transformer cooling is the process of removing the waste heat produced at the transformer winding and safely transferring/disposing that waste heat into the surrounding environment. If we do not remove this waste heat safely and efficiently into the surrounding, the transformer winding insulation can melt and short circuits with excess heat can cause the transformer to explode.
There are several transformer cooling types being developed based on your transformer design, size, capacity, and the industrial standard or requirements. All these methods are specifically designed and only work for a particular transformer and satisfy specific standards.
Contact Daelim TransformerDifferent Transformer Cooling Methods
There are a total of six different transformer cooling methods that have been designed, developed and are being used around the globe. Each method was designed and developed to meet your specific needs and is being used only for specific type, size, and capacity of your transformer.
1. Natural Air Cooling (AN)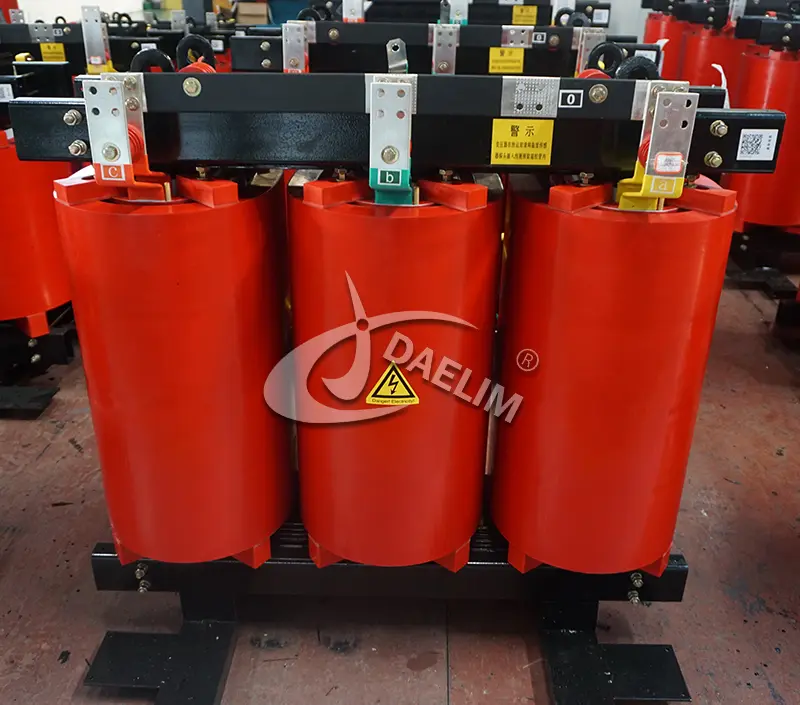
The natural air transformer cooling methods remove heat from our transformer winding through the natural convection of heat into the surrounding air. It is one of the dry type transformer cooling methods and there is no mechanical or special heat transferring mechanism in place to remove heat.
Heat produced at transformer winding is transferred to the surrounding air through the process called free convection. Air then relying on the natural flow of air takes the heat away from the transformer winding.
This method of transformer cooling is only suitable for your small low capacity transformers that do not produce much heat. Heat produced in these transformer windings is never high enough to melt insulation, cause short circuits, or start fires or cause explosions.
2.
Forced Air Cooling(AF)
The forced air based transformer cooling method works very similar to the natural air cooling method. It is also one of our dry type transformer cooling methods. There is only one difference and that is that the air is forced on the transformer winding to remove.
This method also follows the methods of convection to remove heat from transformer winding but its forced convection and these methods remove much more heat and much faster.
A transformer cooling fan is usually installed on the transformer that forces the air to pass through the duct and onto the transformer winding. Faster the air flow over the winding, more heat it will remove and more cooling effect can be produced.
This type of transformer cooling is used in our small to medium capacity transformers where heat generated is enough to melt insulation if not removed. Heat here is not high enough to instantly cause fire or explosion but need forced removal for efficient working.
3. Oil-Based Cooling Systems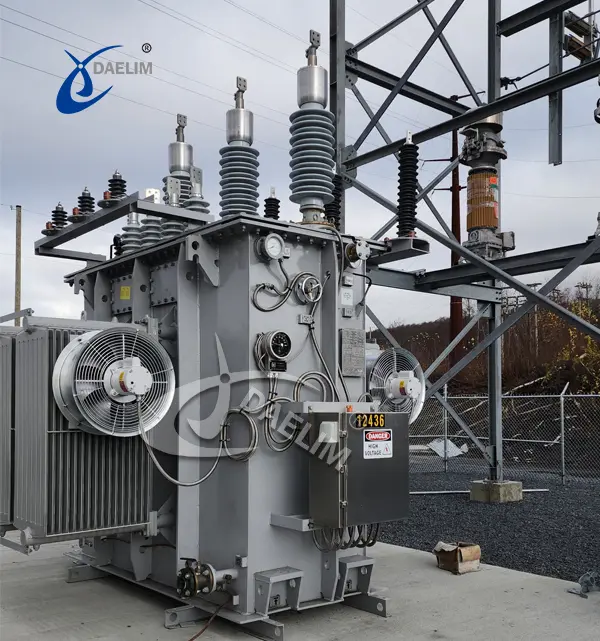
There are two main types of transformer based on how they are cooled. One is dry type transformers where there is no liquid fluid used for cooling purpose and then there are oil type transformers where a transformer cooling oil is used for cooling purpose.
In our oil type transformers, the transformer winding is always kept dipped inside the oil which works as a medium of heat transfer. Winding is placed inside the transformer tank and then the tank is filled up to the top with transformer cooling oil.
Heat produced at the transformer winding during the operation is first absorbed by the transformer cooling oil, heated oil then transfers that heat to the transformer tank that has transformer cooling fins. Then usually free or forced convection is used to remove heat from the transformer tank.
3.1. Oil Natural Air Natural (ONAN)
In the oil type transformer category, oil natural air natural cooling method is the first type that removes heat from transformer winding using free convection methods. Heat produced at your transformer winding is first absorbed by the transformer oil.
Oil absorbs heat using the principle of free convection and then transfers that heat to the transformer tank using the same free convection mode of heat transfer. Transformer tank has specially designed transformer cooling fins that can facilitate heat transfer from the transformer tank to the surrounding atmosphere.
Here this heat transfer is done again using free convection mode of heat transfer where heat from the transformer tank body is transferred to the surrounding air. That is why this method is called oil natural air natural cooling methods, because all cooling is done naturally without any involvement of mechanical mechanism for forced convection.
This method of transformer cooling is only applied to your transformers that produce low heat at their winding. This heat is higher in value than the air natural type transformer cooling method by not high enough to need any force convection. Still heat produced here is enough to cause fire if there is not enough transformer cooling oil inside the transformer tank.
3.2. Oil Natural Air Forced (ONAF)
The second method in our oil type transformer cooling systems is the oil natural air force method. In these methods, oil absorbs heat from the transformer winding using the principle of free convection. Oil once heated high enough starts to transfer that heat to the transformer tank body.
Transformer tank body is specifically designed with transformer cooling fins to facilitate the transfer of this heat from transformer cooling oil to the tank body using the principle of free convection. Once the heat is transferred to the tank body, from there heat is transferred to the surrounding air using a method of forced convection.
In forced convection, air is forced to pass over the tank body and transformer cooling fins at high speed thus quickly removing heat from the tank body. A transformer cooling fan is used to force air onto the tank body and fins. In this force convection, higher the speed of the air passing over the body and transformer cooling fins higher will the heat removed and cooling effect produce.
This type of oil natural air forced methods of transformer cooling is used for your transformers with low to moderate capacity and heat production. Heat produced in these transformers is always high enough to cause fire or explosion in transformer winding if it is not removed properly and quickly.
3.3. Oil Forced Air Forced (OFAF)
Third type in our oil type transformer cooling systems is the oil forced air forced type transformer cooling. In this system two different mechanical mechanisms are used to force the liquid oil and air to remove heat from the transformer winding through the principle of forced convection.
First the heat produced at the transformer winding is removed from the winding by oil through the mode of forced convection. Transformer cooling oil in the transformer tank is forced to move either in circular motion or in a confined path by a heavy duty oil pump. The moving oil when passed over the transformer winding absorbs heat and based on forced convection principle, higher the speed of the oil greater will be the heat removed.
The oil, after absorbing heat from the transformer winding, transferred it to the tank body using the same principle of forced convection. The transformer tank body is specifically designed with fins to facilitate the transfer of heat to and from the tank body.
Heat once transferred to the transformer tank is transferred to the surrounding again by the mode of forced convection. A transformer cooling fan is used to force air to pass over the body and transformer cooling fins of the transformer tank, thus removing all the heat. Same principle of higher the air flow more will be the heat removed will be applied here.
Due to the presence of the dual cooling mechanism for a single transformer, the heat removed in these methods is higher than the previous two oil type transformers. This method is used in all types of heavy duty transformers where heat produced is always high enough to cause serious fire and explosion if the entire transformer is not cooled properly.
3.4. Oil Forced Water Forced (OFWF)
Fourth and most advanced type of oil type transformer cooling system is the combination of oil forced water forced transformer cooling methods. In this method oil cooling is combined with the water cooling mechanism instead of air cooling. This method, like previous methods, used the principle of forced convection to transfer heat from winding to the outer atmosphere.
At first heat generated at the transformer winding is absorbed by the oil throughout the principle of forced convection. Oil is forced to move within the transformer tank by a large oil pump. Faster the oil moves greater and quicker it will absorb heat from the transformer winding.
Oil after absorbing heat from the winding is forced to pass through a separate specially designed heat exchanger. In that heat exchanger, water is used as heat transferring fluid and it absorbs all the heat from the oil through the process of forced convection.
Heat exchanger is usually a shell and tube type heat exchanger where hot oil moves in tubes of the exchanger where water present in the shell surrounds the oil carrying tubes. Heat transferred from oil to tubes to water to the shell and into the outer atmosphere through the process of forced convection.
This type of cooling system is used in specially designed transformers for specific applications where performance and system reliability is top priority. This method does offer higher efficiency and performance in transformer cooling but has high maintenance and operation cost. Heat exchangers need regular inspection and continuous maintenance for optimal performance.
Factors Affecting the Selection of Cooling Methods
Each transformer is different and so is the area of its application. There are three main factors that affect the selection of cooling methods for any transformer.
Transformer Type and Capacity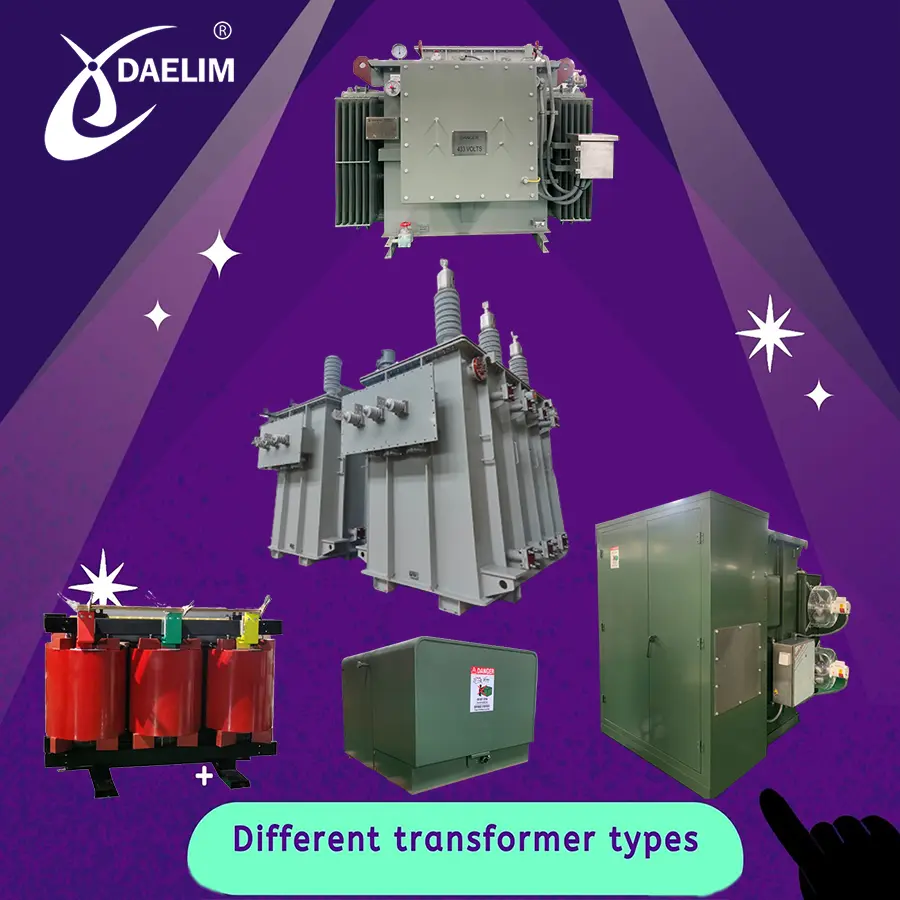
Your transformer cooling method depends a lot on the type and capacity of the transformer. Whether you have a dry type transformer or need an oil type transformer and what power regulating capacity you need from your transformer. More the power regulation needed from the transformer bigger will be its size, more will be its capacity, and greater will be the heat produced at the transformer winding. To remove more heat, the transformer needs an appropriate cooling system.
Environmental Conditions
Second important factor here is the environmental condition in which your transformer is installed. If a transformer is installed in a cold environment where temperature usually remains very low throughout the year, then that transformer does not need a big efficient cooling system. Opposite to that if even a small transformer is installed in a region whose temperature remains high all around the year. Then that transformer will need a proper cooling system to avoid fire or explosion.
Budget Constraints
Installing a specific cooling system to any specific transformer adds cost to the transformer. So it depends a lot on your budget constraints for any project or market value of any specific transformer that which transformer cooling system will be installed on.
Conclusion
Effective transformer cooling is crucial for achieving high performance and reliability in transformer operation. Depending on the heat produced by the transformer winding either air cooled or oil cooled system is used. Both systems can be used in either free convection or forced convection mode, all depending on the transformer requirements. Selecting any specific transformer cooling system depends on the transformer size, capacity, environmental conditions and budget constraints. By addressing challenges and adopting advanced solutions, the reliability and efficiency of transformers can be significantly enhanced.
Follow Up
Efficient transformer cooling is such a critical factor for reliable transformer performance. At Daelim Transformer we offer high quality transformer cooling systems of all types. We can deliver you a transformer of any size, capacity, power rating, and with any dry or wet type cooling system.
At Daelim Transformer we follow all national and internal standards of transformer manufacturing and safety including but not limited to ANSI, IEEE, CSA, AS, GOST, IEC, EU, and DIN/VDE. We have fully functional distribution and facility centers and a strong customer base in the USA, Europe, Canada, Australia, and all others around the globe.
If you have any query about transformers winding, just Contact Us and we will talk you through the process.
Related Products
Related Article
The ultimate guide to ONAN transformers
ONAN is a form of transformer cooling in which mineral oil is used inside the transformer tank to cool and cool the transformer. KNAN is another cooling method for transformers, which means that vegetable oil is used to cool the transformer inside the oil tank.
Transformer Shortage: Factors and Challenges of Current World Order
The global shortage of electrical transformers is driven by increased demand due to lifestyle shifts, population growth, and industrial expansion, particularly in electric vehicles, cryptocurrency mining, and AI data centers. National policies, supply chain disruptions, raw material shortages, and manufacturing constraints further exacerbate the issue. Daelim offers industry-focused solutions, leveraging multiple production facilities to meet demand and provide high-quality transformers in record time.
VPI Transformer vs Cast Resin
VPI and Cast Resin transformers are both dry-type transformers with distinct characteristics. VPI transformers use vacuum pressure to impregnate resin for enhanced insulation and moisture resistance, making them ideal for moderate environments and industrial applications. Cast Resin transformers, with solid epoxy resin construction, offer superior durability and fire resistance, suited for harsh environments like marine and mining. VPI transformers are cost-effective, while Cast Resin models have higher upfront costs but longer-term reliability.
How To Check Transformer Primary And Secondary?
Transformers are essential for regulating electricity in homes and industries. Proper inspection of transformer windings—primary and secondary—is crucial for ensuring safety and performance. Tools like multimeters and insulation testers help detect issues such as open circuits, short circuits, and insulation breakdowns. Regular maintenance prevents catastrophic failures, enhances safety, and extends transformer life, ensuring reliable operation across global installations.
How Long Does It Take To Replace A Transformer
Replacing a transformer involves several steps, including inspection, equipment transportation, removal of the old transformer, and installation of the new one. Smaller transformers can be replaced in a few hours, while larger industrial or utility transformers may take days or even weeks. Factors such as transformer type, site conditions, weather, and availability of parts can influence replacement time. Proper planning ensures efficiency.
The Ultimate Guide to Transformer Voltages
Transformers are essential for regulating voltage in power systems, ensuring safe and efficient electricity distribution. They come in various voltage ranges, including low, medium, high, and extra-high voltage for different applications, from residential use to heavy industrial operations. Understanding transformer voltages—such as 240V, 480V, 600V, and renewable energy-specific voltages like 600V and 800V—is crucial for optimizing performance and preventing equipment damage in sectors like manufacturing and energy.