Understanding Types of Transformer Winding and Their Applications
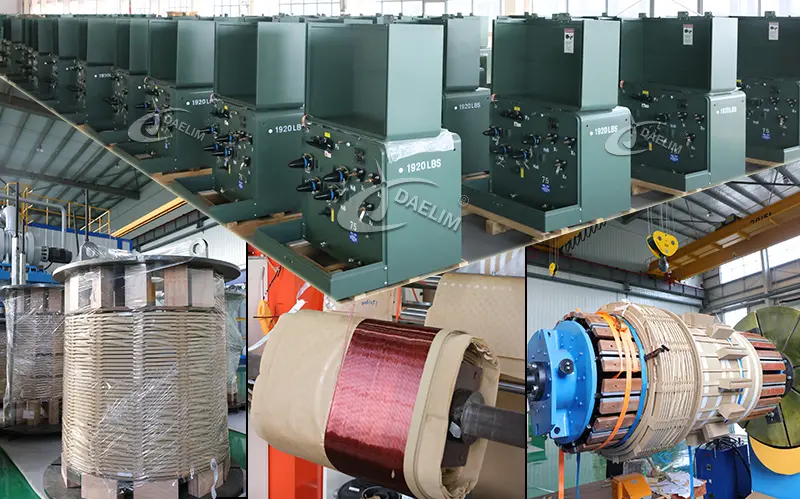
Transformers use different winding types to maximize efficiency, cooling, and performance for various applications.
In this article, you’ll discover types of transformer windings in core type and shell type transformers, including disc, helical, sandwich, and crossover windings.
We’ll break down each type’s unique structure, cooling benefits, and practical applications, so you can understand how different transformer winding can serve your needs.
Contact Daelim Transformer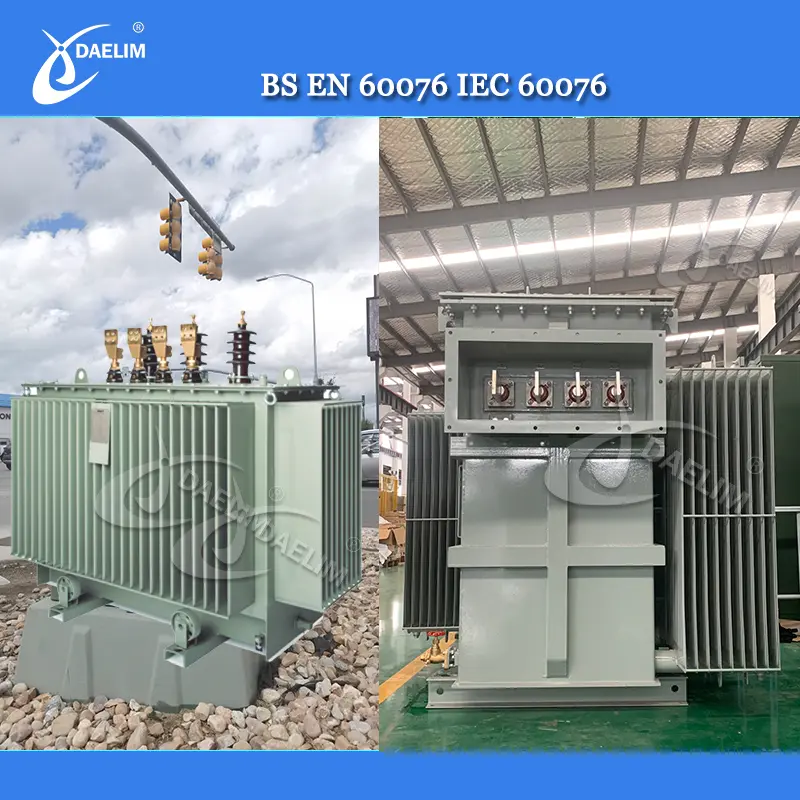
ECO design transformer(Tier 2) complies with the latest energy efficiency standards of the European Union, and has silicon steel core and amorphous alloy core transformers. Designed and produced according to IEC and BS standards, it is energy-saving, environmentally friendly and highly efficient.
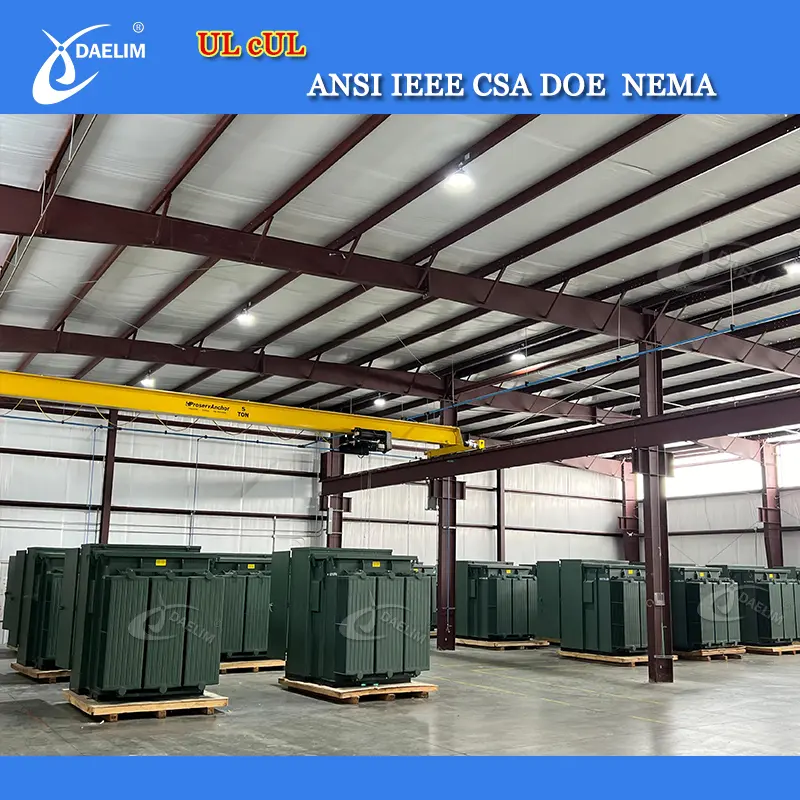
At our facility in Houston, we have hundreds of transformers in stock, including pad-mounted transformers ranging from 300 kVA to 3000 kVA, with voltage levels of 12.47, 13.2, 13.8, 24.94, and 34.5 kV. We also offer single-phase transformers with capacities from 50 to 175 kVA. There's no need to wait—immediate shipment is available!
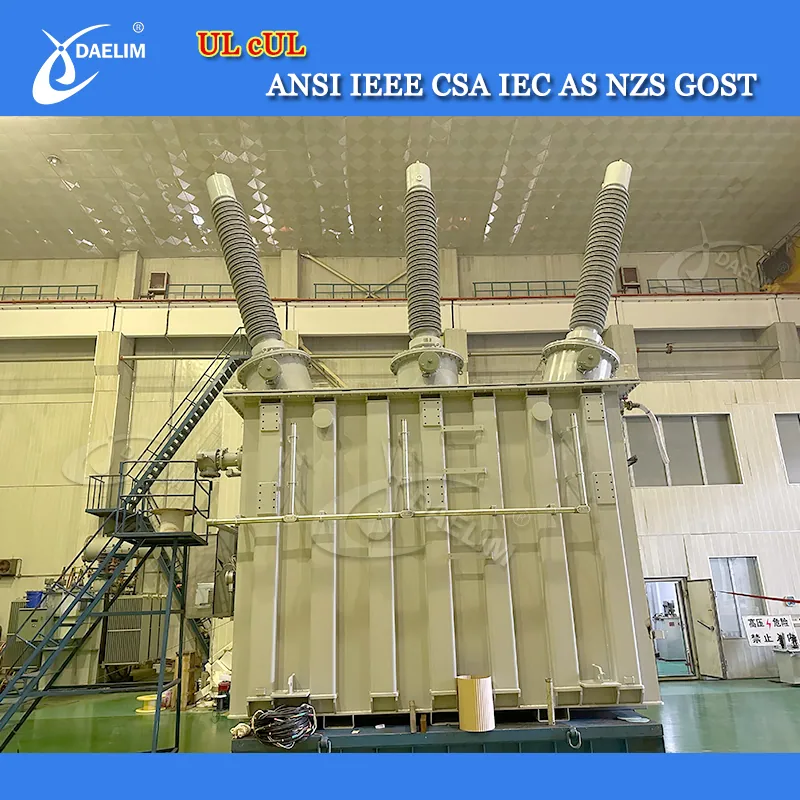
Daelim Transformer offers a complete line of oil-immersed transformers that meet current applicable standards, including IEC, IEEE, ANSI, CSA, NEMA, AS/NZS, and GOST. Our high-voltage power transformers are available for voltages up to 230 kV and ratings up to 300 MVA. We have successfully supplied hundreds of high-voltage power transformers across America.
Common Types of Transformer Winding
At DAELIM Transformer, we use different transformer windings for different functions and configurations.
Windings are arranged to produce a magnetomotive force (MMF), which the core transfers to other windings to achieve different voltage levels.
Broadly, transformers are classified into two main types based on their core structure and winding arrangement:
- Core type transformer
- Shell type transformer
In our core type transformer, you’ll see the winding wrapped around the core. In contrast, with a shell type transformer, the core itself encases the winding.
Our winding design considers factors like current rating, short-circuit capacity, temperature limits, impedance, surge voltage, and transport requirements.
How About Transformer Winding Type For a Core Type Transformer?
Helical Winding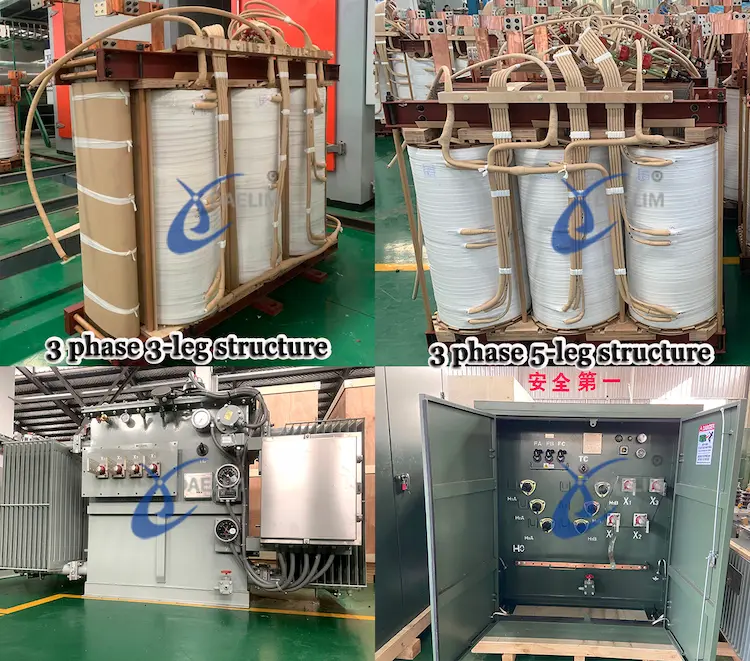
Helical winding comes in four forms, single, double, disc-helical, and multi-layer. We use helical winding in our low-voltage, high-capacity transformers.
It is made up of rectangular conductor strips wrapped in helix form, positioned radially in parallel layers.
Each turn spans the full radial depth of the winding. We use the utmost 16 parallel strips to make a conductor.
Generally, we use four types of helix winding in our power transformers:
- Single Helix Winding: We orient single helical windings in an axial direction, following an inclined, screw-like path. Each winding has a single layer of turns, offering a streamlined design suited for low-voltage applications.
- Double Helix Winding: Double helical winding minimizes eddy current loss by reducing the number of parallel conductors. The design enhances transformer efficiency and reduces overall energy loss.
- Disc Helical Winding: We arrange strips in parallel and side by side along the radial direction to fully cover the winding’s radial depth.
- Multi-layer Helical Winding: We utilize this type of winding in our high-voltage transformers with ratings of 110 kV and above. We use multiple cylindrical layers, concentrically wound and we connected them in series.
Cylindrical Winding
For our low-voltage transformer with a power rating of 600-700 kVA and a current of 10-600 A, we use cylindrical winding.
We apply cylindrical windings in their multi-layer form. Rectangular conductors are used in a two-layered type to secure the lead-out ends.
The layers of the windings are separated by oil ducts, allowing for effective cooling as oil circulates throughout the winding structure.
Continuous Disc & Disc Winding
We mainly apply disc winding in our power transformers as it facilitates a reliable transformer design. For the winding, we use discs or flat coils arranged in either series or parallel.
We create the coils from rectangular conductor strips, wound in a spiral pattern outward from the center in a radial direction.
One or more strip conductors are wound in parallel along the flat side, lending strength and durability to this winding style.
Each disc is spaced by sectors attached to vertical strips, while additional spacers create radial and axial ducts.
This design allows oil to circulate directly around each turn, facilitating efficient cooling and maintaining optimal transformer performance.
The advantage you get from disc and continuous disc winding is greater mechanical axial strength and affordability.
Crossover Winding
On many occasions, we apply this type of winding in the high-voltage winding of our small transformers.
We separate the layers of winding 0.5 to 1 mm and ensure the voltage is maintained at 800 and 1000.
Normally, the crossover type of winding has more strength compared to the cylindrical type of winding. Also, don't forget that crossover wind has lower impulse strength than cylindrical.
You will also incur more labor costs when using a transformer with a crossover type of winding.
Types of Transformer Winding For Shell Type Transformer
Sandwich Type Winding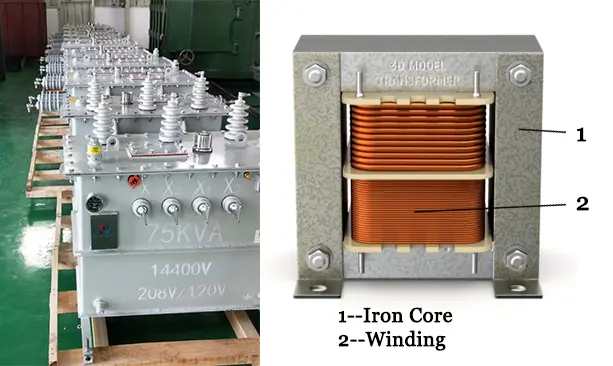
In sandwich windings, primary and secondary windings are arranged in alternating layers, basically “sandwiching” them together.
The design enables the windings to share the magnetic field, enhancing transformer efficiency and reducing energy loss.
We ensure equal ampere-turns in each winding to balance the magnetomotive forces in the sections.
More resource: Why does transformer require a balanced winding?
Increasing the degree of subdivision reduces the overall reactance, resulting in improved electrical performance.
Benefits of Shell Type Winding in Transformers
- Enhanced Insulation: The core's structure provides superior insulation for windings, increasing safety, especially in high-voltage applications.
- Reduced Leakage Flux: The core surrounding the windings confines magnetic flux, minimizing leakage flux and promoting higher efficiency.
- Improved Mechanical Strength: A robust core structure offers strong support, reducing the risk of damage from external forces or short circuits.
- Compact Design: The core-enclosing structure results in a more compact transformer, ideal for space-limited installations.
- Better Heat Dissipation: The core helps spread heat, enhance cooling, and prolong the transformer's lifespan.
- Higher Efficiency for Low to Medium Power: Particularly efficient in low to medium power applications due to reduced energy losses.
- Better Short-Circuit Withstand Capability: Even distribution of magnetic forces in the shell design increases resistance to short circuits, improving fault tolerance.
Conclusion
In a nutshell, various types of transformer windings serve specific operational needs by optimizing efficiency, cooling, and mechanical strength.
In core-type transformers, helical and cylindrical windings are often used to handle varying currents and maintain effective cooling for low to medium-voltage applications, while disc windings support high-capacity transformers with added durability.
Shell-type transformers use sandwich windings, where primary and secondary windings are layered to reduce energy loss and improve insulation.
The design limits magnetic flux to minimize leakage and provides a compact, sturdy structure ideal for high-stress environments, making these transformers more efficient and reliable.
When choosing a transformer manufacturer and supplier, choose DAELIM Transformer for our certified solutions. Our services are UL/CUL, and CE certified.
FAQs
1. What are the main types of windings in power transformers?
The main types of windings in power transformers include helical, disc, and cylindrical windings, with each type offering specific benefits for voltage, current capacity, and cooling.
2. What is winding in transformer?
Winding in a transformer is the coiled conductor that creates magnetic fields. The fields help transfer electrical energy from one winding to another, allowing voltage transformation.
3. What is the purpose of layer winding in transformer?
Layer winding refers to coils stacked in multiple layers to manage higher voltage and increase insulation, allowing safe operation in transformers that handle high voltages.
Related Products
Related Article
What Is An NLTC Transformer and How Does It Work?
An NLTC (No Load Tap Changer) transformer efficiently adjusts voltage levels while de-energized, ensuring stable power supply in manufacturing and industrial applications. By manually changing the transformer’s turn ratio, NLTCs maintain optimal voltage without interrupting operations. Their simplicity, reliability, and cost-effectiveness make them ideal for systems with infrequent voltage adjustments. Discover Daelim's NLTC transformers for enhanced energy efficiency.
How to Choose Transformer Supplier
Choosing the right transformer supplier is crucial for ensuring stable power supply and efficient operations. Start by identifying your specific transformer needs, researching potential suppliers, and evaluating their quality and reputation. Consider pricing, customer support, and delivery logistics. Ultimately, trust your instincts and maintain open communication to establish a strong partnership. Discover reliable solutions with Daelim for optimal energy usage.
A Guide to Tier 2 Transformers
This article discusses the EU's Tier 2 Ecodesign Regulations aimed at reducing transformer energy losses. By enhancing design and materials, these regulations lower CO2 emissions and operating costs. DAELIM Transformer is highlighted as a leader in producing compliant, high-efficiency transformers that support sustainability and improved energy performance.
How Transformer Components Function Together to Control & Deliver Electricity
This article provides an overview of the key components of transformers and how they work together. It discusses the functions of transformer windings, cores, insulating materials, and transformer oil, as well as the roles of cooling tubes, tanks, and safety features. Overall, these components ensure effective voltage regulation and safe electricity delivery.
Why Is Transformer Oil Change Important?
This article emphasizes the importance of transformer oil changes for reliable transformer operation. Transformer oil provides insulation, cooling, and protection against moisture and oxidation. Regular replacements prevent moisture accumulation, oxidation, and particle contamination, ensuring safety and efficiency. Key steps for an oil change are outlined, highlighting the benefits of routine maintenance, including enhanced reliability, extended lifespan, and reduced operational risks.
Transformer Design: Step by Step Guide for Safety and Reliable Power Flow
This guide outlines the step-by-step process for designing transformers, covering key stages from requirement analysis to testing and production. It highlights the importance of adhering to relevant standards like IEEE, IEC, and ANSI, and emphasizes the selection of materials, winding design, cooling systems, and insulation for efficiency and safety. Proper mechanical design, protection devices, and thorough testing are critical for ensuring reliability and performance. The guide concludes with the importance of accurate documentation and continuous improvement in transformer design for long-term efficiency and durability.